BROOKS, WV
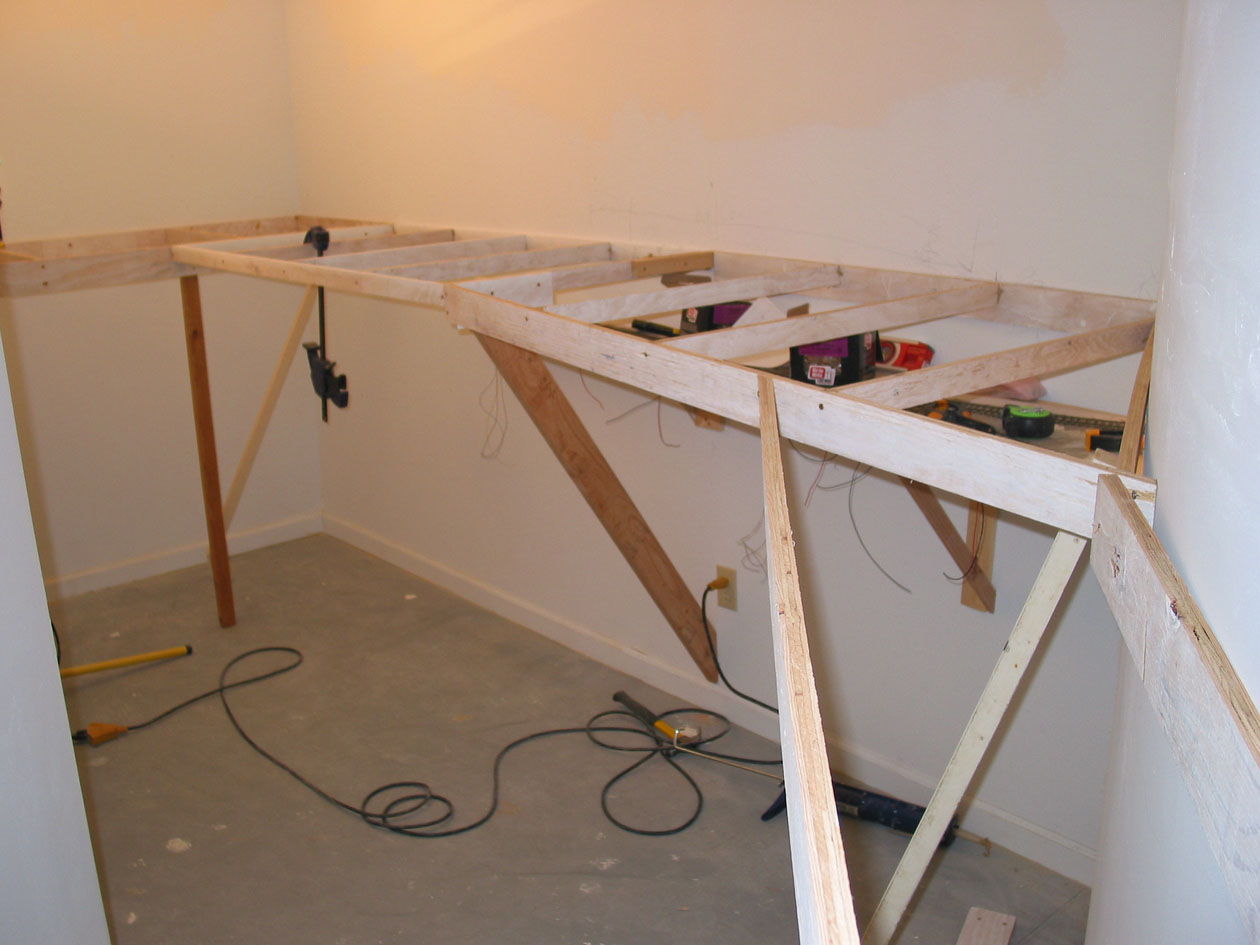
Brooks, WV (so named for our late crew member Bob Brooks), began as some wood framing at the end of the Kayford Coal Branch.
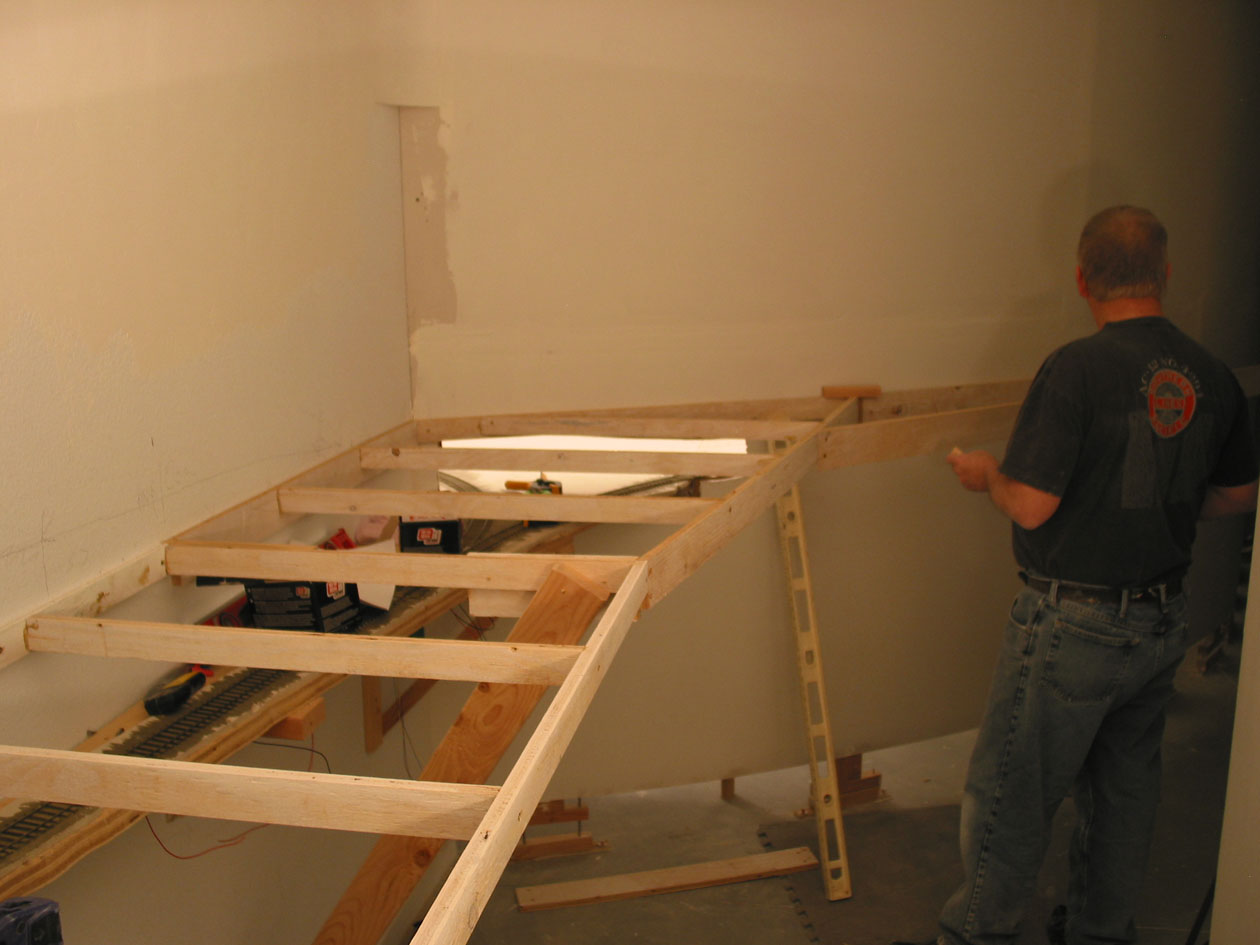
A look back at the angled wall which will come into play as Brooks gets imagined and its coal loadout considered. The tail of the TA Tower Wye in wall-adjacent Ricksburg is seen below Brooks.
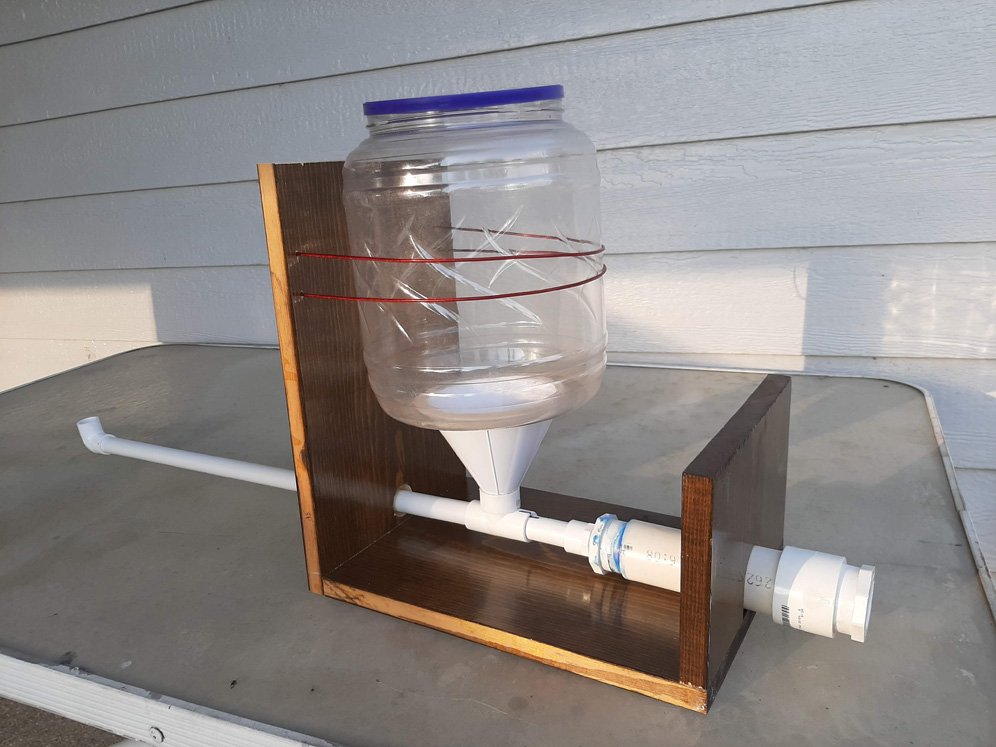
Wanting a way to refill a coal reservoir above and behind a mountainside without the requirement of reaching high up and over scenery, and before any construction began, I devised a system for blowing the “coal” (black-dyed Harbor Freight course Black Walnut shells - i.e. sand blasting grit) up a PVC pipe and into the mountain reservoir. The exhaust side of my shop vac does the trick. A clay venturi at the PVC Tee speeds up the air stream to help with the push. A brass slide gate at the base of the funnel has since been added to cut off the flow of coal at the start and stop of each filling. It worked! Now what kind of working coal loader do I want to build?

From my Bob Helm “Clinchfield in the Coal Fields” book I’d long admired the Clinchfield Coal’s Crooked Branch flood loader on the Haysi Branch. With its long conveyor feed to the top of the load reservoir it seemed like it could be the perfect fit for Brooks. It was.

The tube enclosed conveyor comes from inside the mountain. Perfect!

Lots of visible detail to this loader as well. It looked like an explosion of an Evergreen Styrene rack waiting to happen, with hoppers to boot!

With the model selected, it was time to construct reservoir first (working the scene from back to front). An internet search yielded a wide funnel for the planned reservoir and a small discharge port. Would it get the job done?
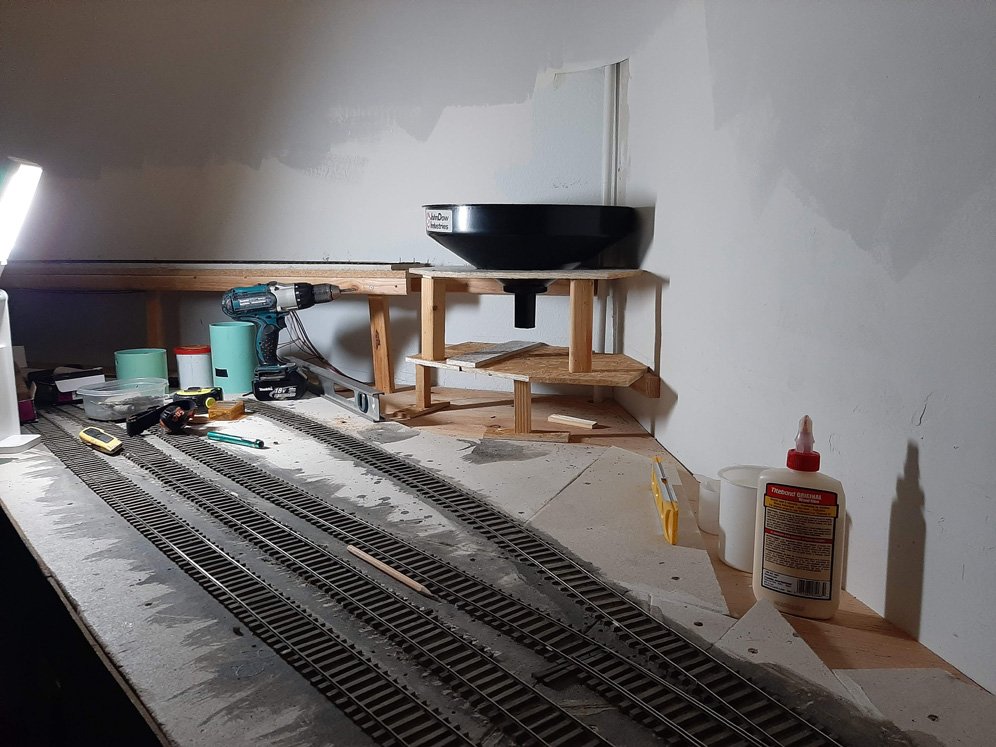
Support framing was constructed to hold this industrial funnel, with a platform below for mounting the end of the conveyor and its drive motor.

Next was the conveyor itself. A strip of leftover house trim (save everything) with styrene shields on each side formed the basic structure. A stretched black elastic waistband formed the conveyor belt. The drive motor went on this end with a knurled and beveled drive drum (thanks Bob).
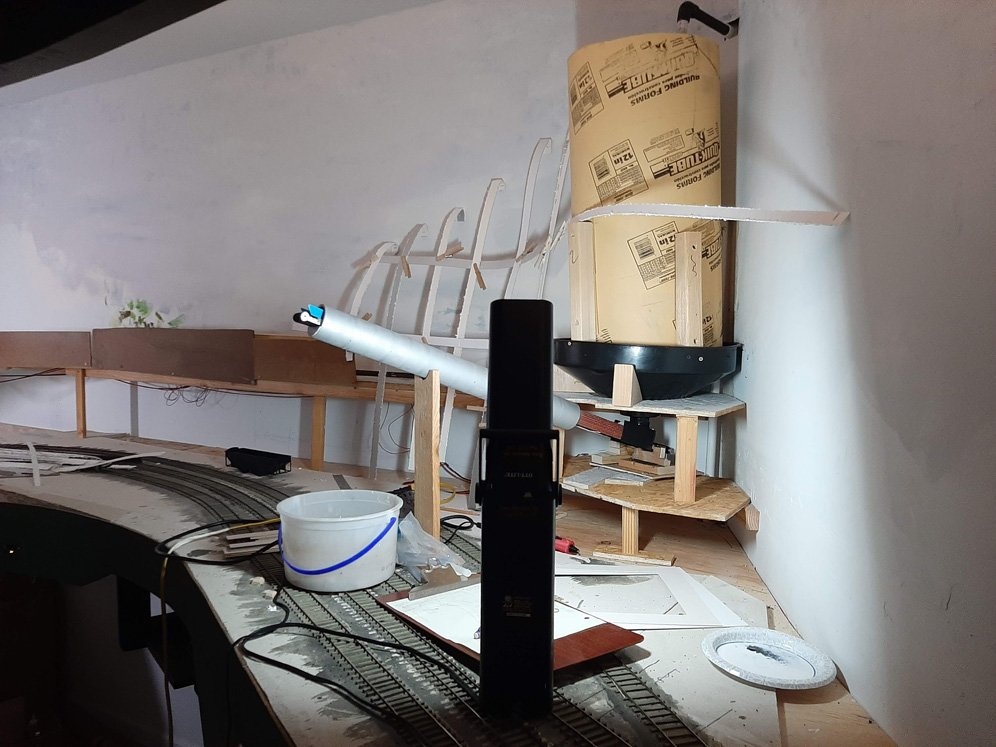
A Sonotube (Home Depot- used for concrete pilings) serves as the coal reservoir. I secured it to the funnel and excitedly dumped coal in it, ready to fire up the drive motor and conveyor it out. And it did….for awhile. But…
The funnel proved to be too wide such that the black walnut shell coal simply locked together and wouldn’t slide into the discharge port. DOH!
Of note too is that a small PVC pipe is tucked into the wall corner, rising behind the reservoir. Its two-elbow bends direct the flow of coal down into the tube. To let the vac exhaust air escape and keep coal from sprinkling onto the entire scene, the waistband of a pantyhose (thanks Katie) was stretched over the top of the tube with the PVC passing thru one of the legs. A rubber band secured the leg around the PVC :) Problem solved.

Back to the drawing board. An interior funnel was added to the inside of the Sonotube with poster board, and this with a steeper profile.

Is this the discharge side of a jet/rocket engine? No, it’s the poster board funnel being firmly supported and secured on all sides by triangular pieces of foam core hot glued in place. Now, let’s try the flow again.

BINGO! And up the conveyor belt it goes….on and on. Mountain forming webbing is starting to enclose the reservoir.
The tracks along the wall that abut the funnel are C&O staging from the adjacent room and the town of Linnwood. How to keep them accessible? You’ll see.
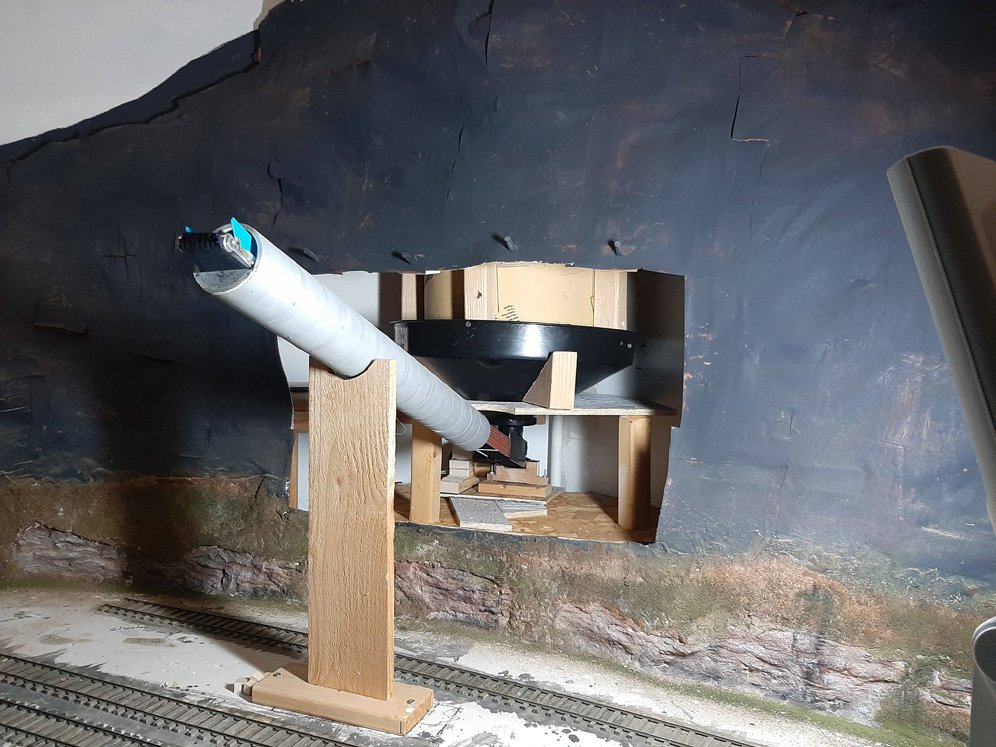
The mountain side now encases the reservoir. Of note is that the discharge end of the belt has a ball bearing drum to reduce friction. An aluminum painted PVC pipe with styrene details added as per the prototype now encases the conveyor. A temporary wood support stands in place of the eventual steel support.
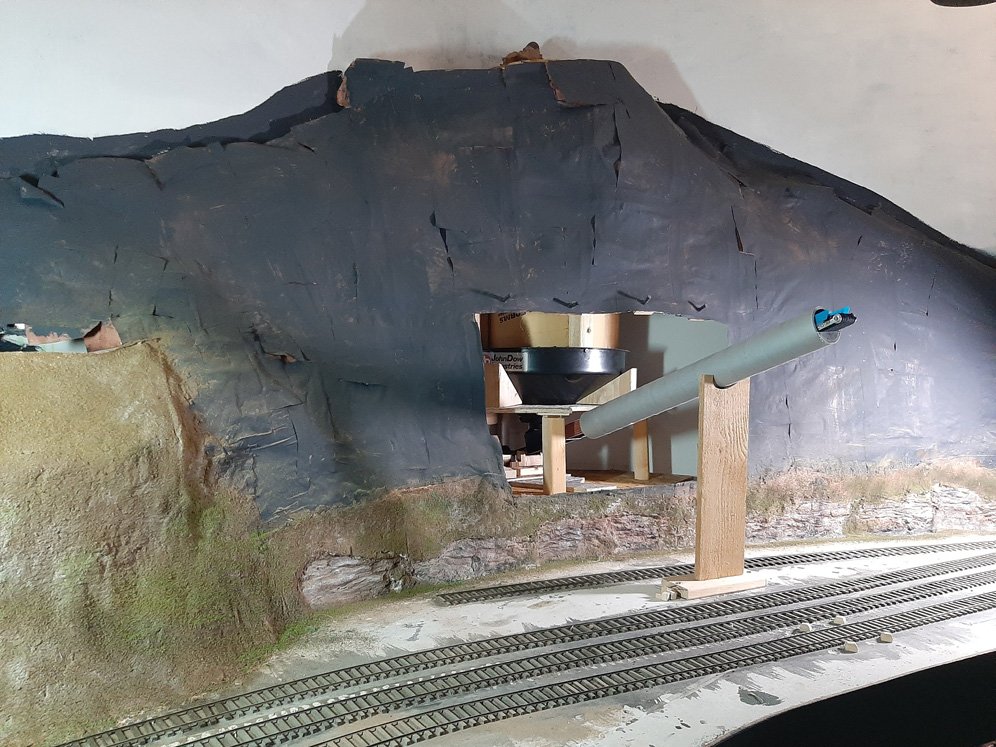
We’re already a long way from that wood framing we started with.
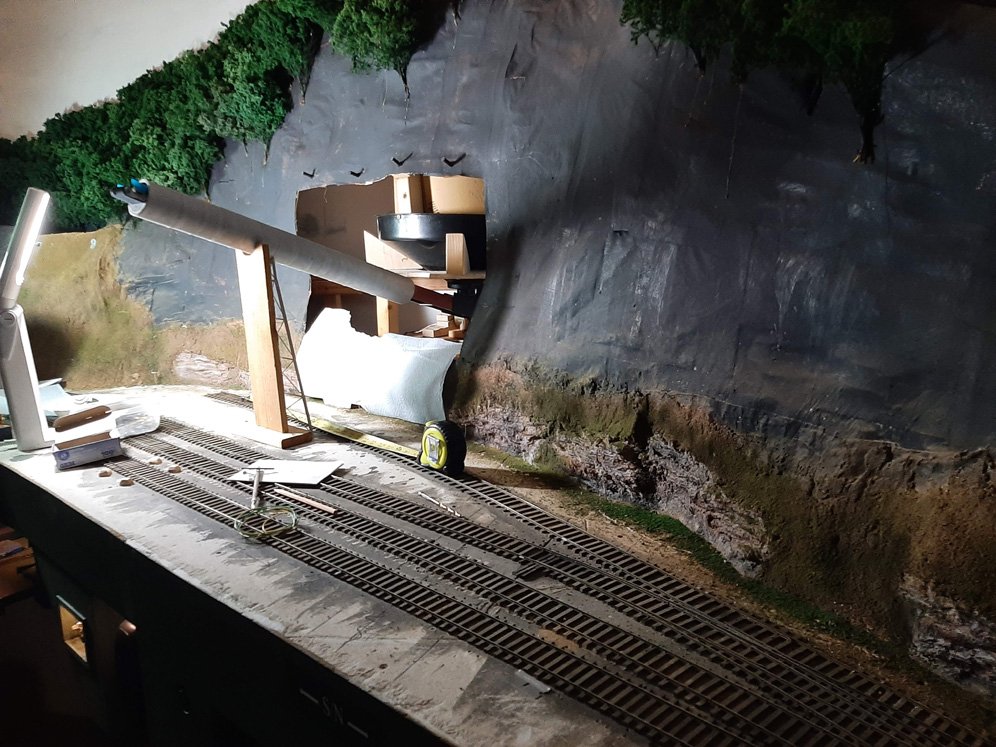
Hydrocal rockwork has been added and trees are starting to populate the hillside. Just barely visible on the lower left are the new controls for flood loader.
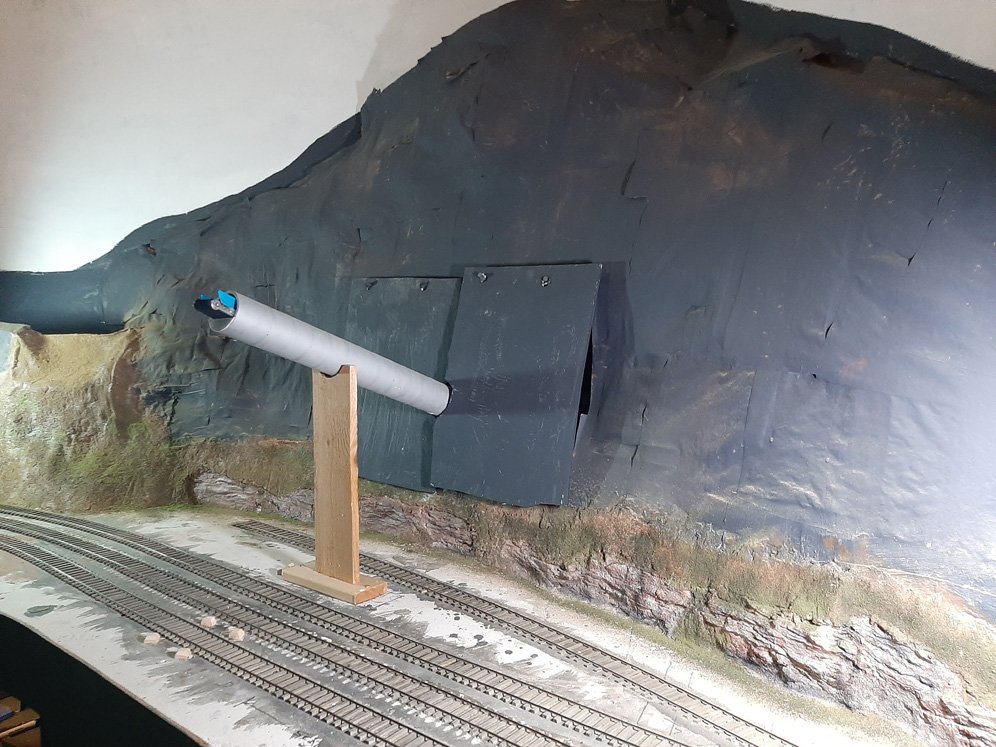
Time to make the removable panels that hide the drive mechanism. Two matte board pieces meet at the conveyor. Trees will be added to them to make them invisible to anyone but ME.
Note the concrete footings for the loader have now been located spanning the front track.
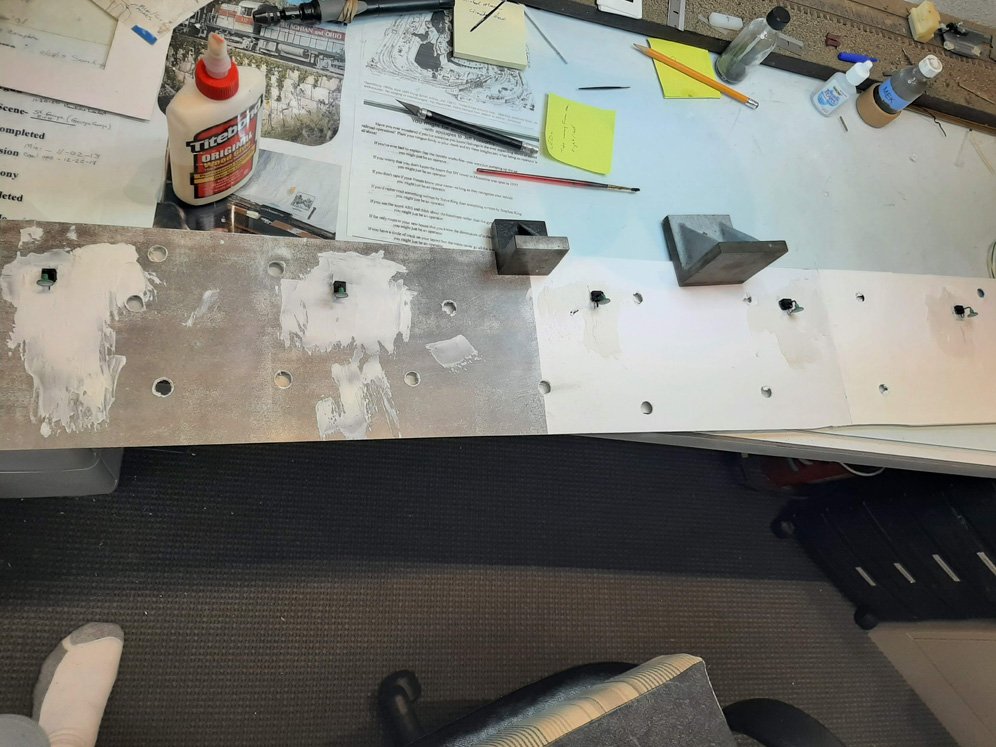
Two tracks come into Brooks thru a 3’ tunnel. Switching crews will need to access this space frequently enough that it seemed prudent to add lighting to the tunnel interior (oh shoot).
This is the visible interior tunnel wall with its 5 spaced LED lamp-shaded lights is under construction. The lamp goosenecks carry the LED wires to the backside for power attachment.
The wall is styrene (I buy it by the 4×8’ sheet) and the random holes are for anchoring the tunnel “concrete” drywall mud to the styrene. Small hooks were added under each lamp fixture to eventually hold looping wires thru the tunnel. Details.
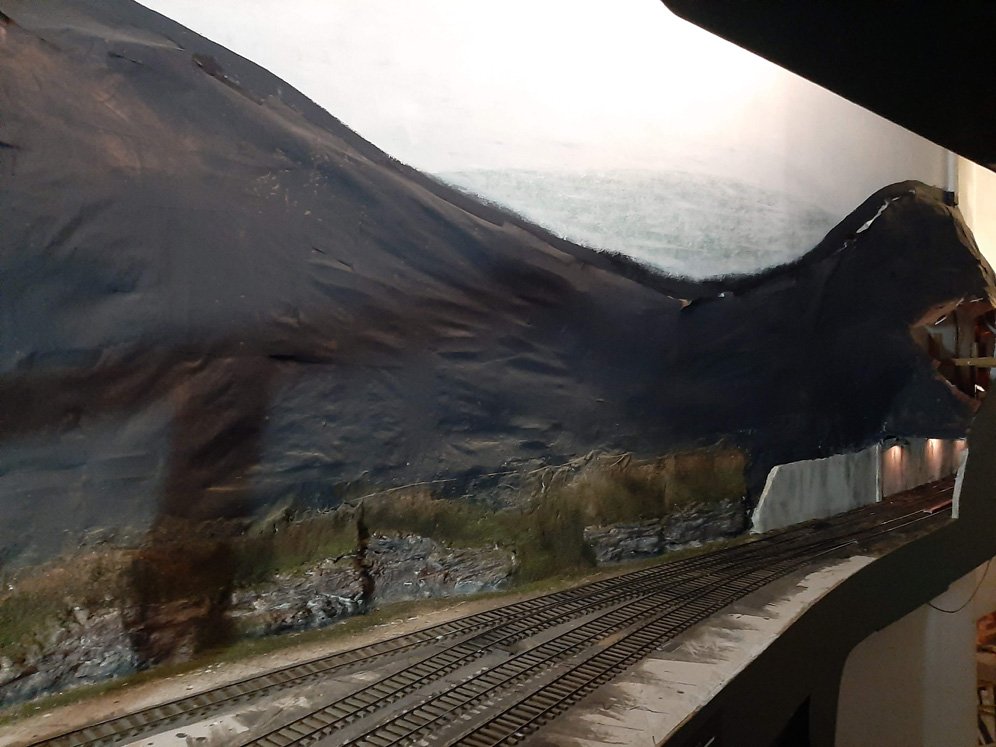
A distant shot showing the now lighted tunnel entering the hamlet of Brooks, WV
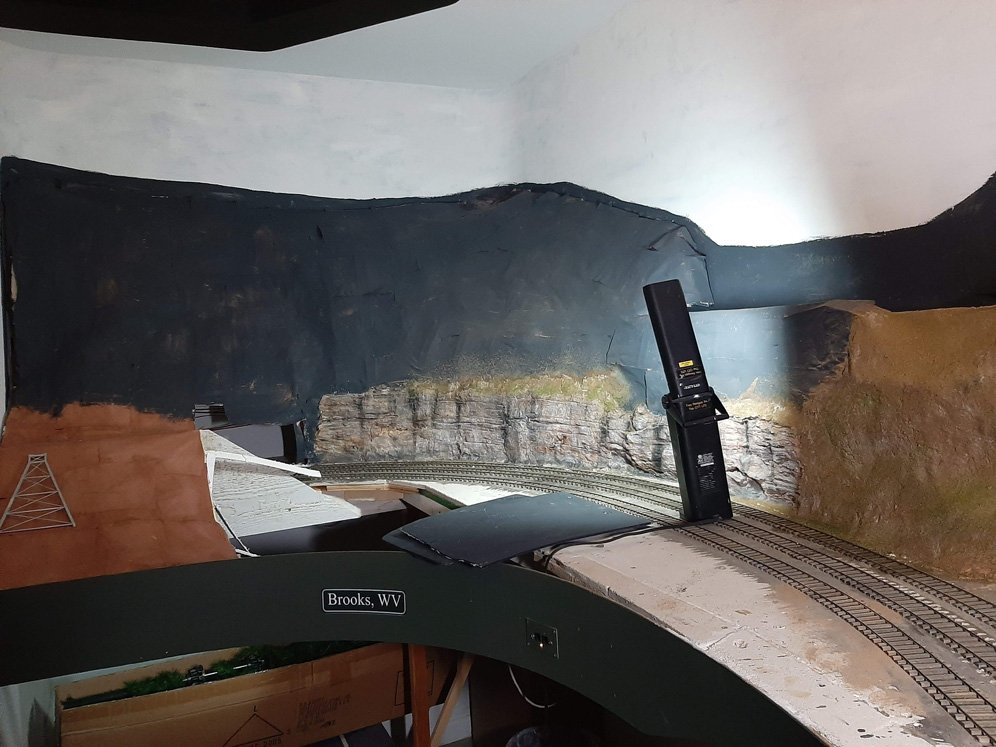
The tail tracks from the loader curve out of view behind a future hillside festooned with a small town and company houses- Brooks, WV.

Glue still drying, more trees!
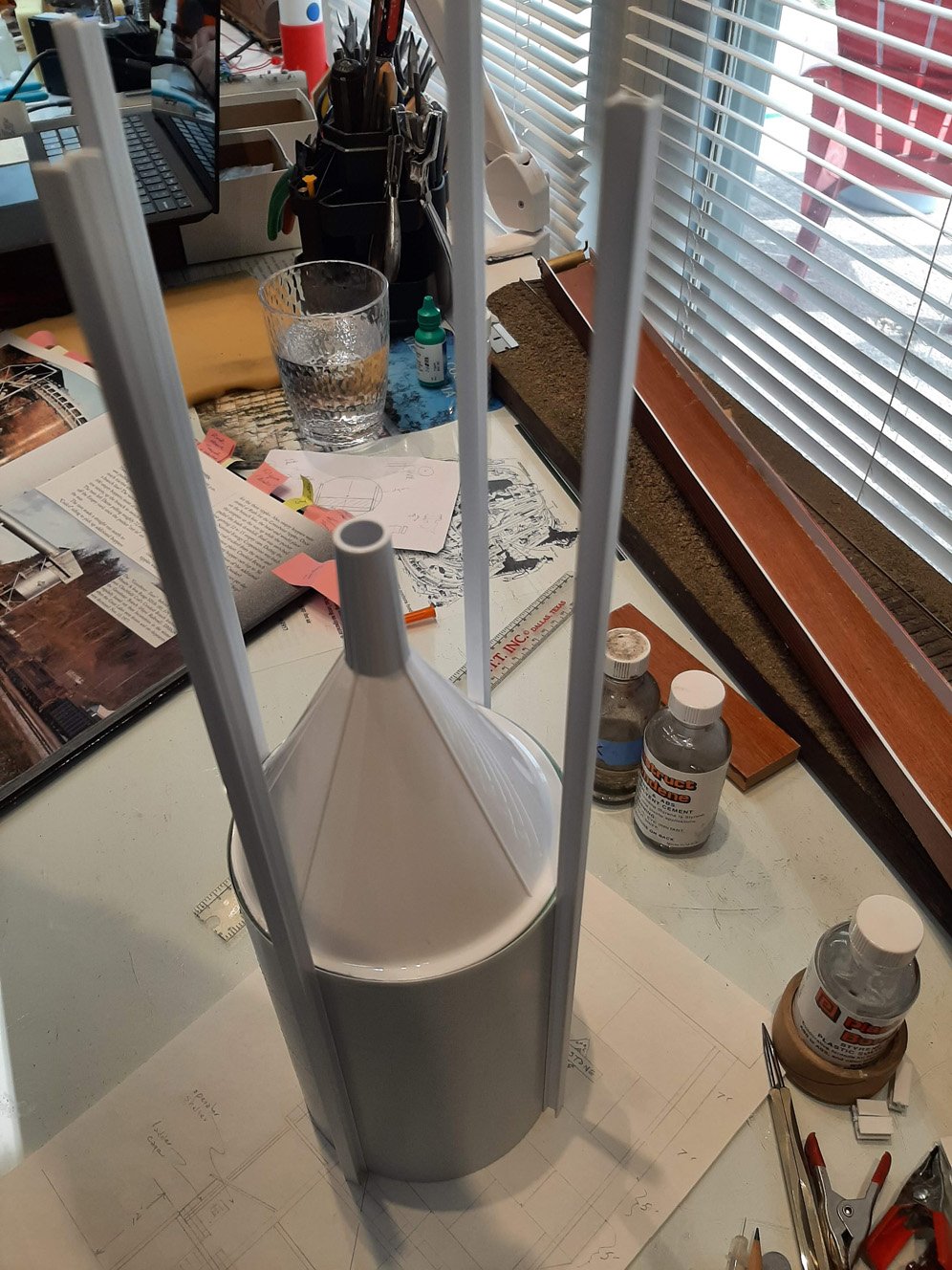
Time to build the loader. 4” PVC Perf pipe formed the cylindrical reservoir. .010 styrene was embossed with rivet detail and glued on, with the mating seam facing to the rear. The prototype’s funnel became a 4” kitchen funnel; a perfect fit! A Chute was made, H-beam legs, cross-bracing. etc., etc. At least I had pictures to work from.
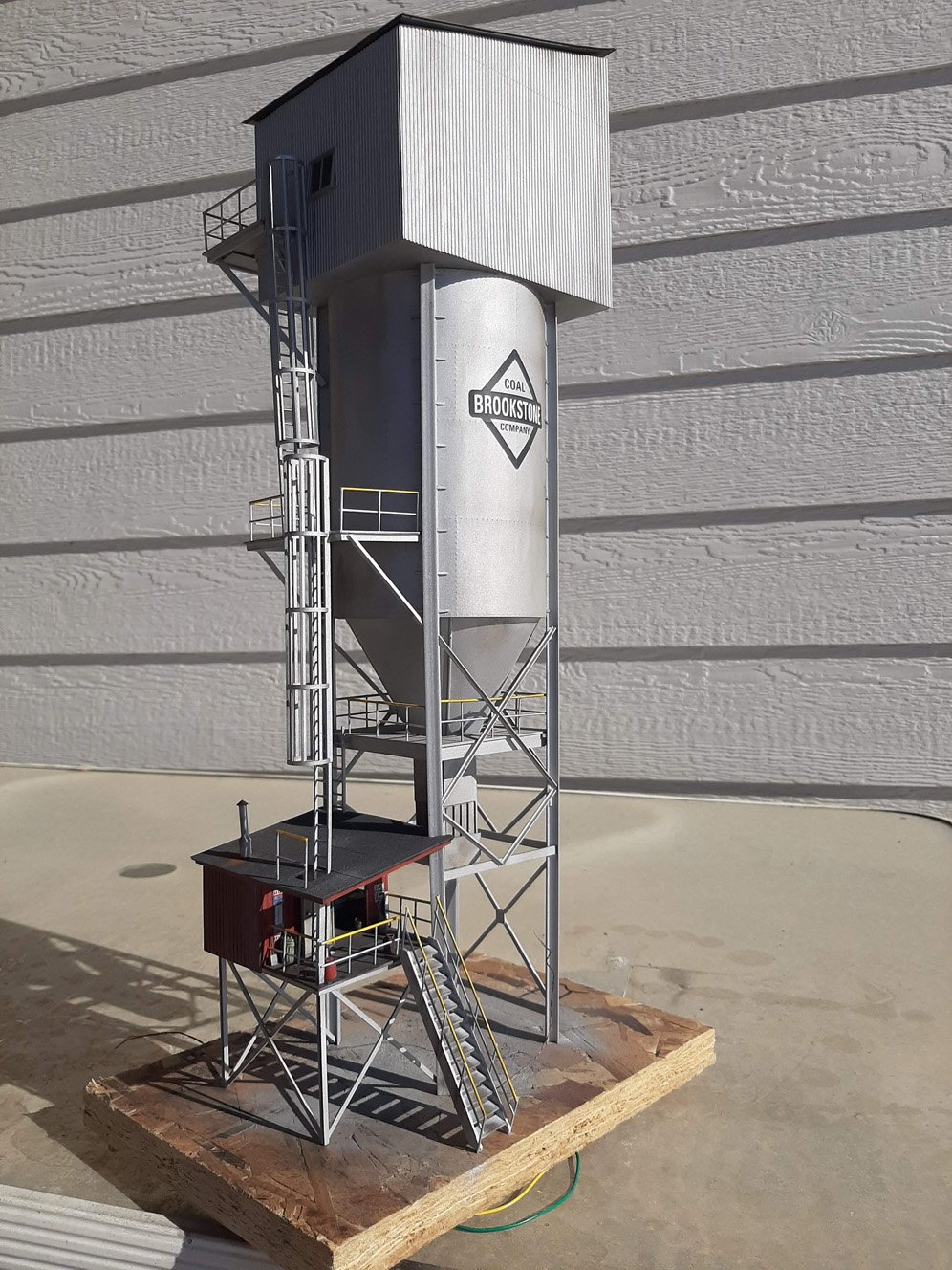
Many hours later, the finished product. I decided to name this loadout Brookstone Coal Company- in honor of Bob Brooks as well. Roughly following the prototypes lettering, Bob Sobol printed up decals to mimic the real thing. Sweet. Compare this and the next photo to the proto pix.

A fun project.
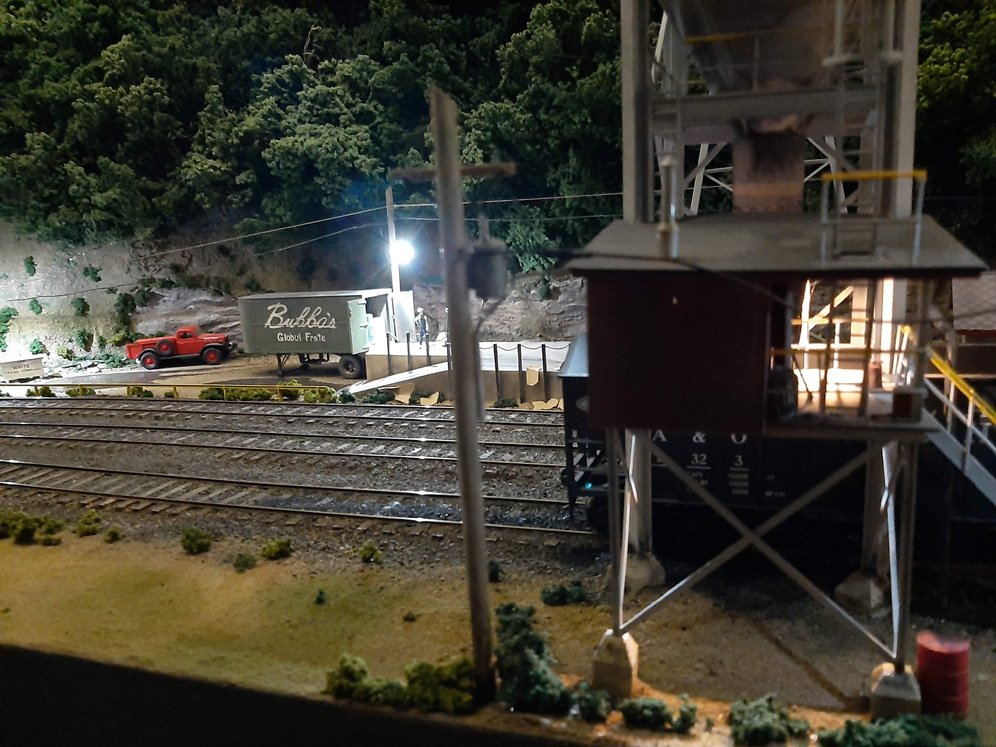
LED lighting in the misty, dimly lit Brooks scene really adds to the operator experience.

Flood loader Seymore watches as each car passes beneath the chute, dispensing the coal in proper amounts. Not quite visible here is that he also has a couple jugs of Moonshine near his desk. That must explain the spilled coal I find after operating sessions. Hmmm.
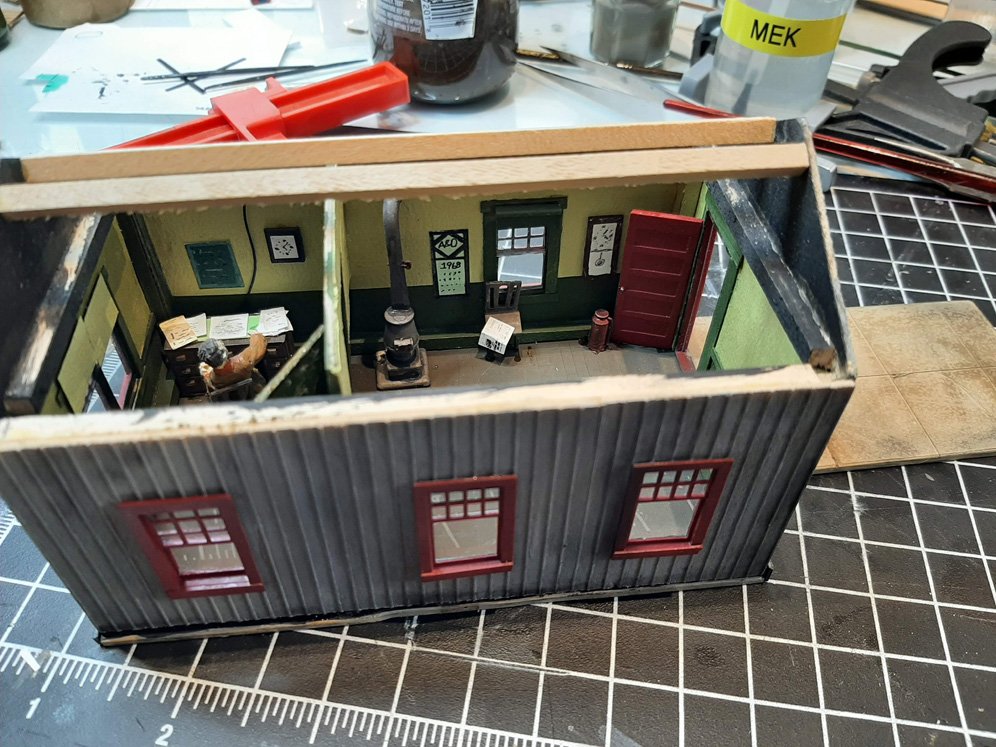
Twice a day a doodlebug visits the town of Brooks as it services the Kayford Valley hamlets. So, a small station was needed. It also serves as the location for the Kayford Dispatcher who issues track warrants for the train crews. The Kayford is “dark” territory.
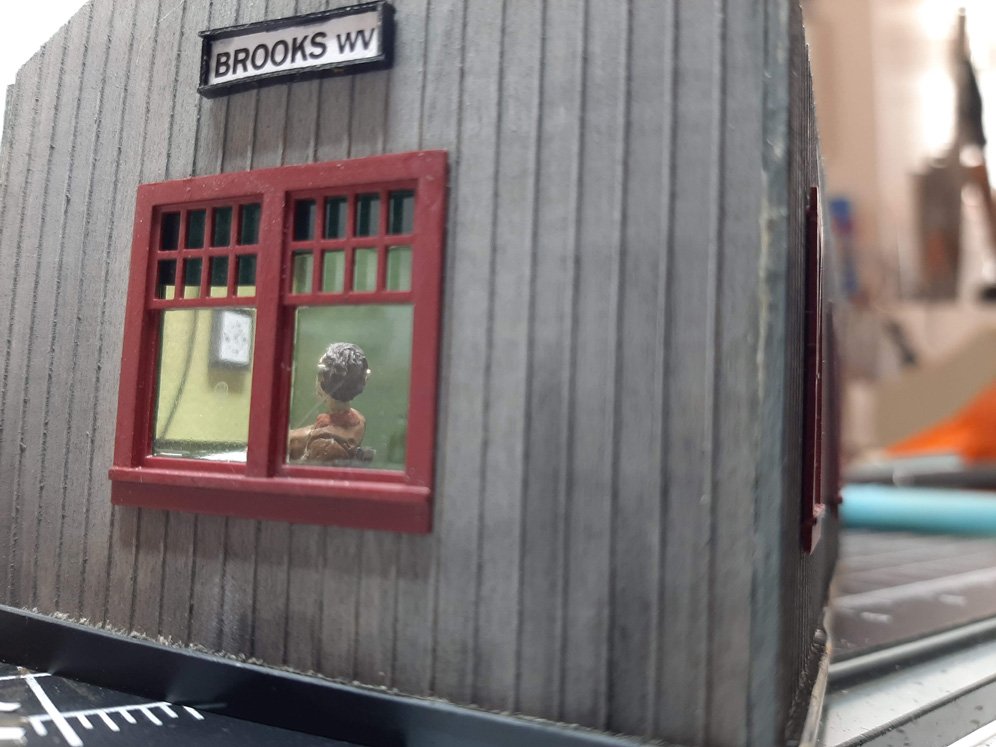
Kayford DS Jim Bob sits by the phone and looks at this time sheet.
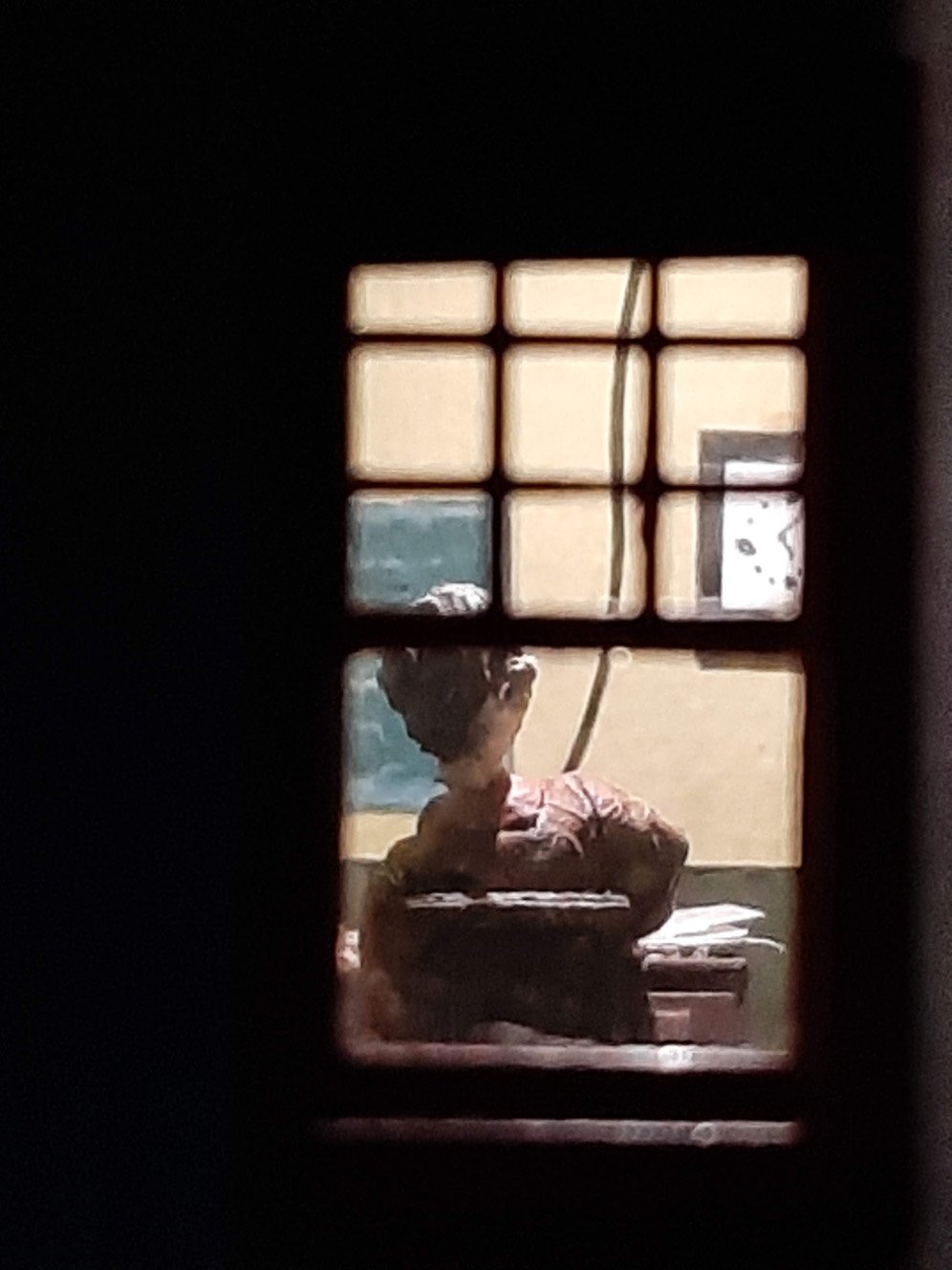
The wall clock says #400, the Scarlet Shifter should be about here. Hmmm. Who was on that crew today anyway?
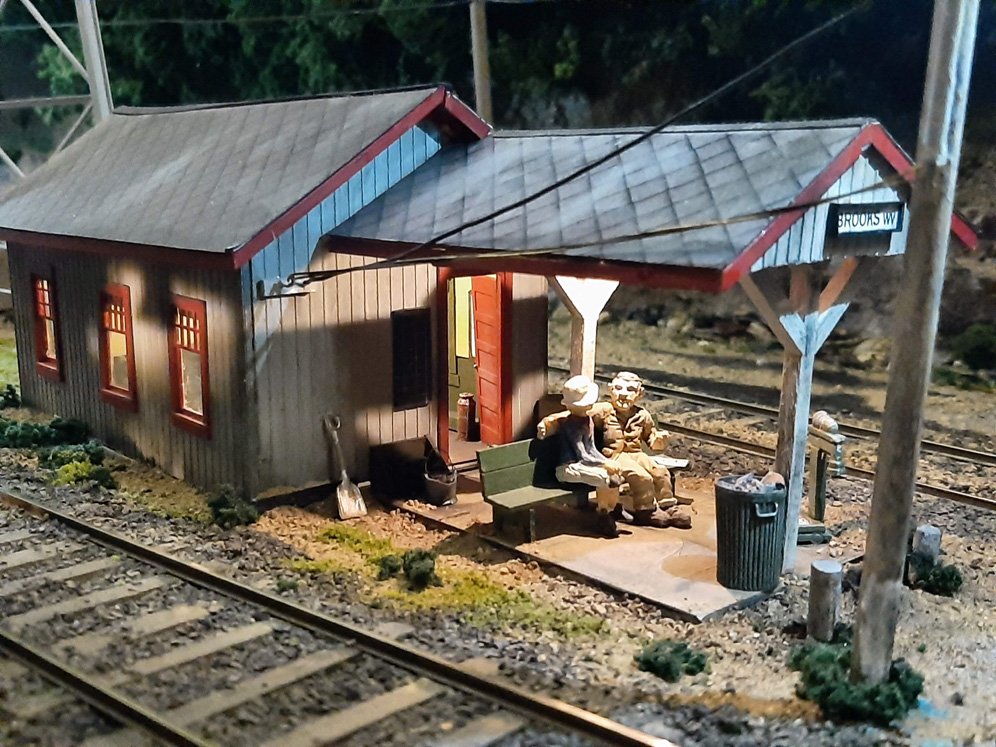
Billy Bob sits with his cousin Bonnie Sue, making time with her until the Bug arrives. He just couldn’t make himself wait for the family reunion to find a date.

A now out-of-service scale house sits on the approach lead to Brookstone. Siding is by Clever Models, a paper print over styrene, and windows by Grandt Line. Imagination by David Stewart.
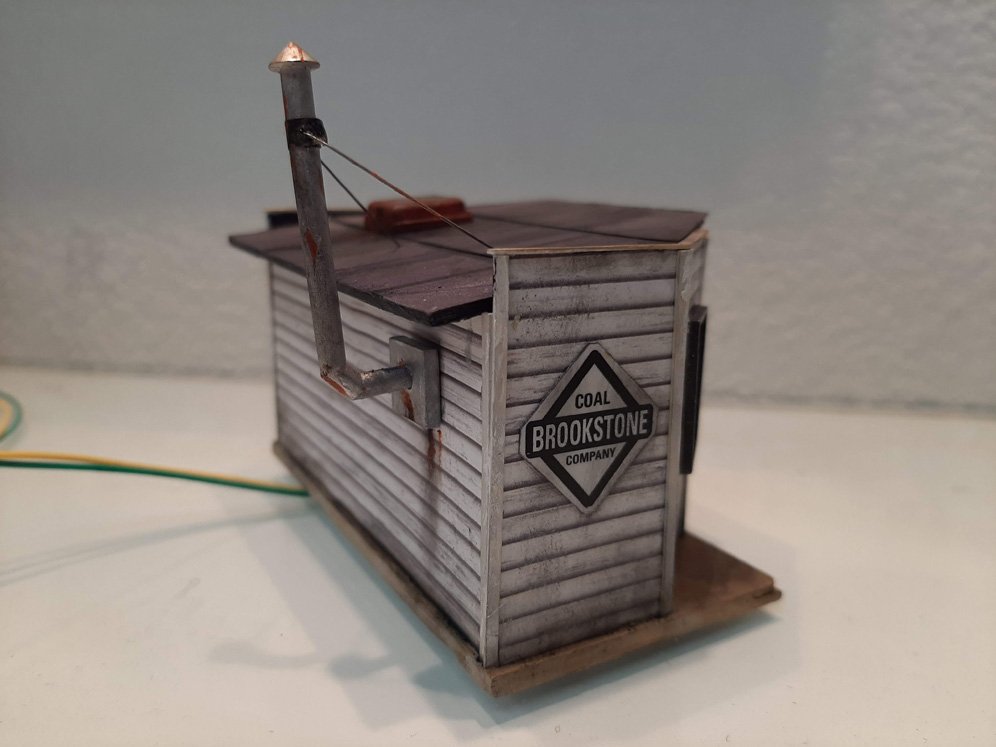
What the engine crews see.

What the Brookstone/Kayford DS sees during an op session. The old switch points for this bypass scale now lay behind the scale house. No need to have them still mucking things up.
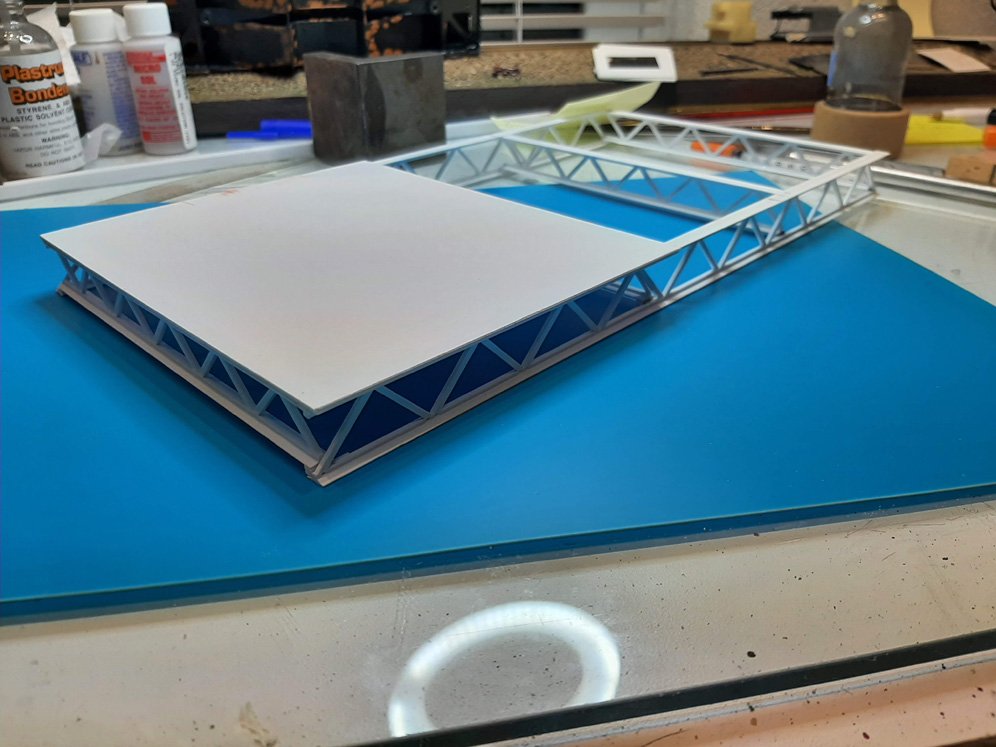
Brookstone isn’t the only coal game in town. It also features the “K.O. Dorff & Son Coal Company”- courtesy of Kirk and W. Kirk (Jr.) Orndorff A&O crew members. As with so many Appalachian coal loadouts, it is also unusual in its footprint.
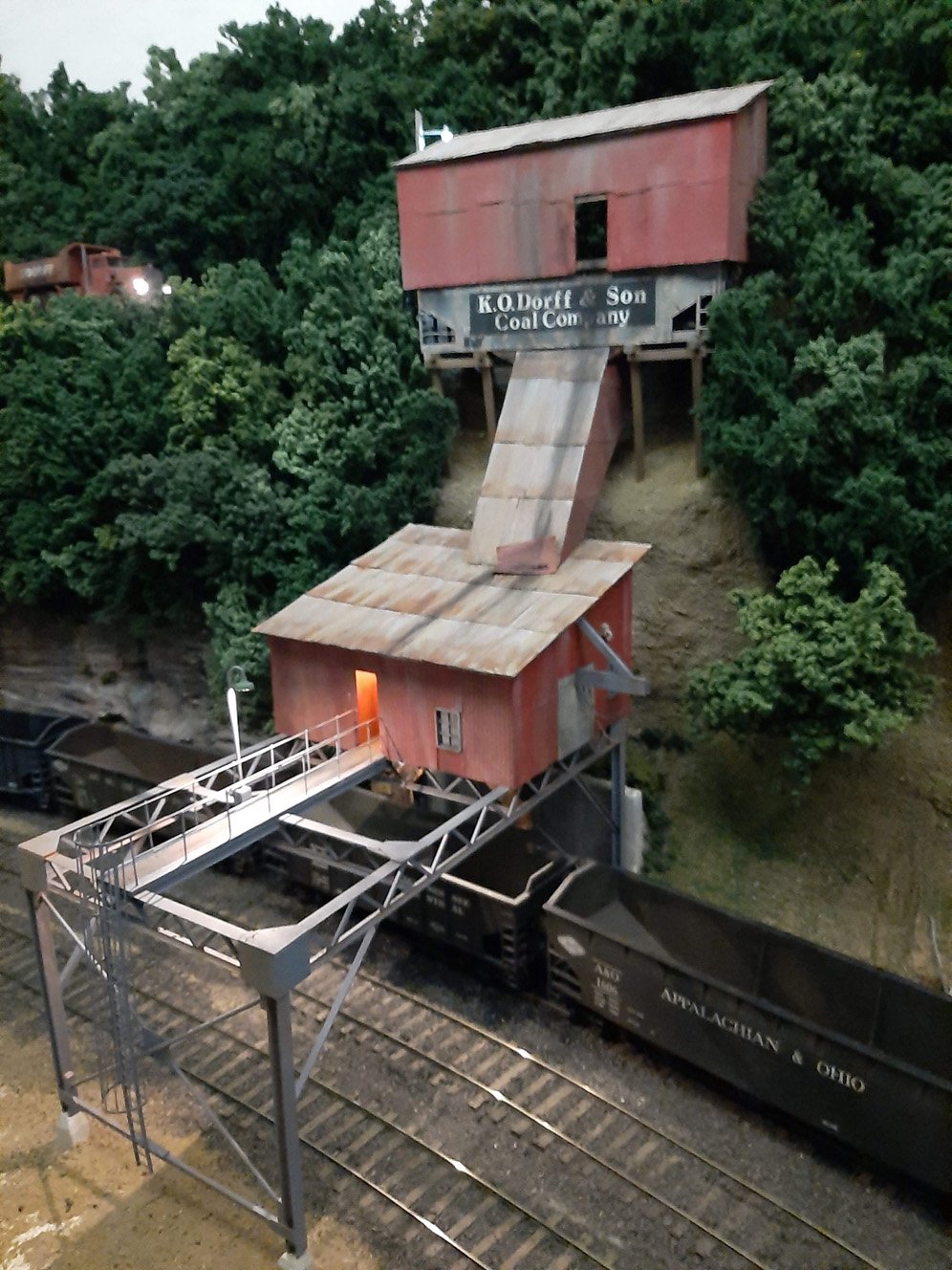
Based on a loadout in Pikeville, KY, an old coal hopper on stilts and serves as the dump pit for the stream of K.O.Dorff & Son trucks dumping their diamonds. Personel access to the Dorff loadout was a challenge, but they got it done.
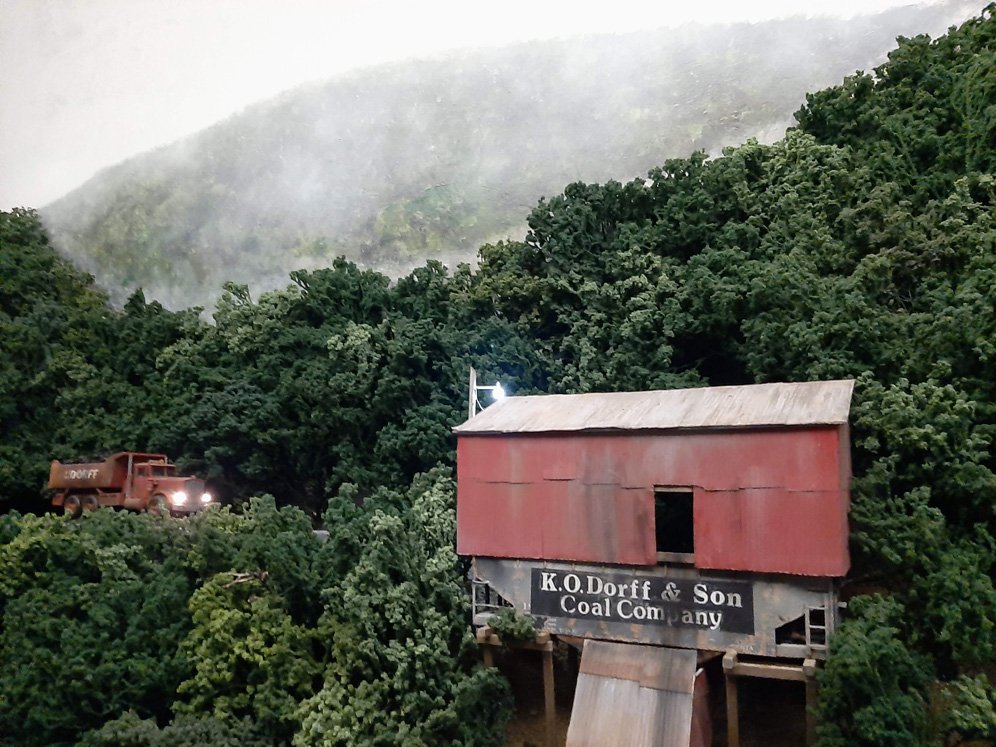
The rain is still misting on this late August early morning as a truck approaches, headlights still on.
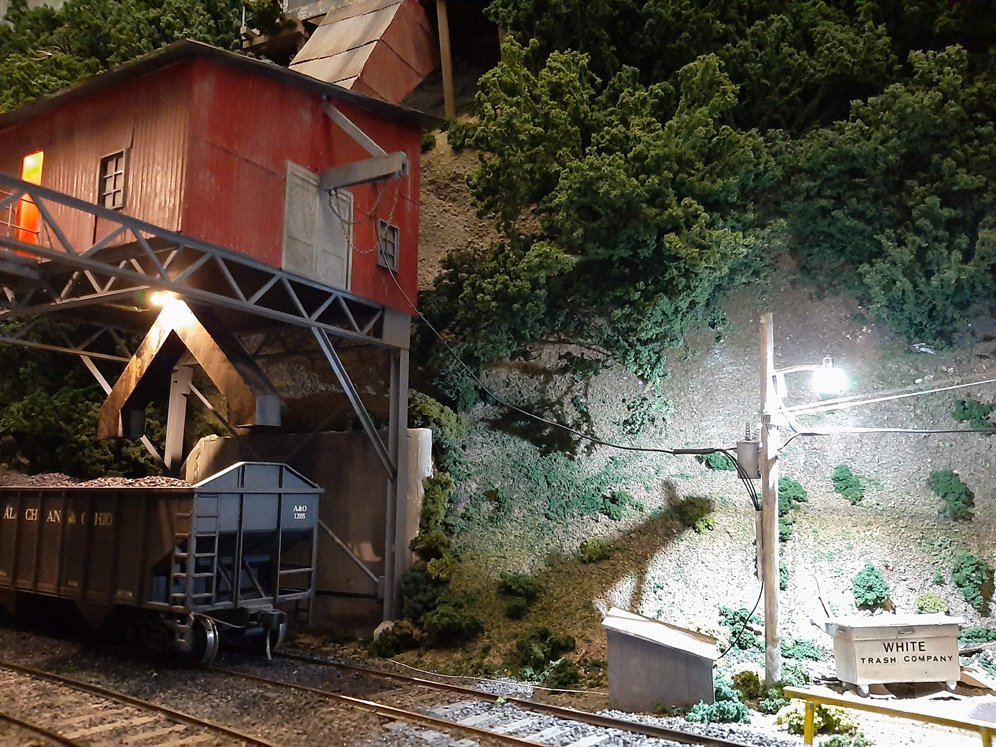
A car puller winches hoppers under the Dorff chutes. Dorff is a “static” loader- the hoppers are loaded either between op sessions for pickup, or more often, they are loaded at Brookstone and placed under the chutes for later pickup. This particular coal turn is numbered 911, and is referred to as “The Dorff Dash.” :) The “White Trash Co” also pays a visit here.

Oh yes, the C&O staging track. It turns out they are accessible, if need be, behind the tree covered hillside. In fact, the Dorff Coal truck sits on a cross-track piece of matte board. Who knew?!

The Bug station track ends at loading dock, providing an “industrial” spot for the Kayford Local. Styrene construction, of course.

A Lionel 32’ curved nose van with opening doors provided a customer for the Team Track.

Bubba has grand expectations for his trucking business, better than his spelling grades.
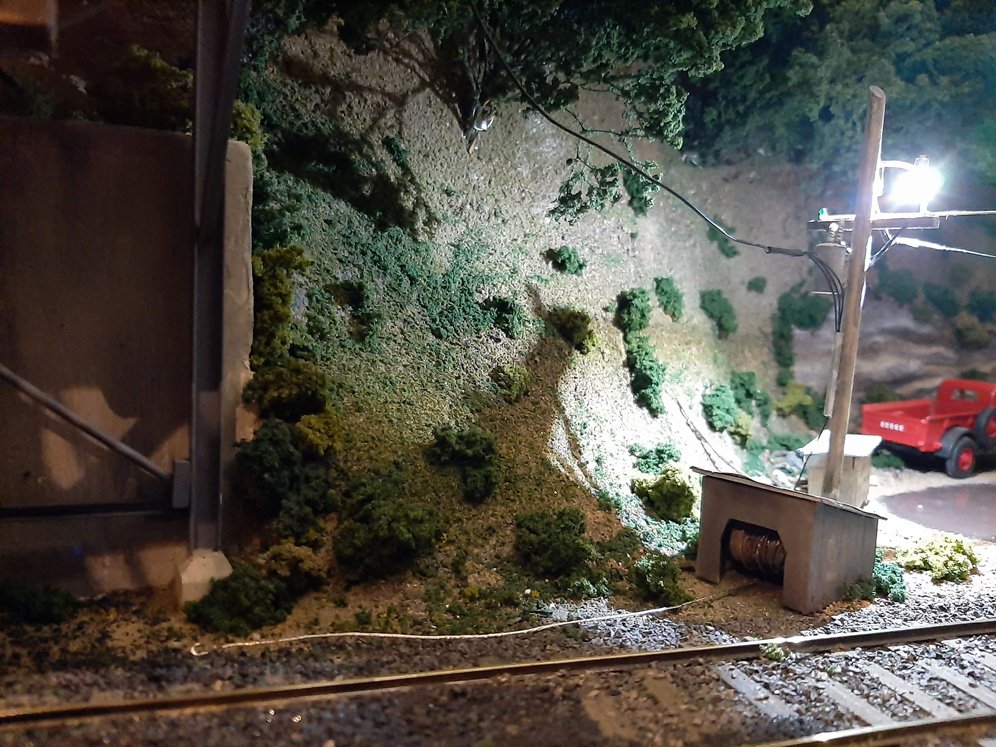
Steel cable lays on the ground at the Dorff car puller.

Scattered mercury vapor lights help to navigate this darkened scene. Here are the two tracks and tunnel mentioned earlier than lead to Brooks on the Kayford Branch.
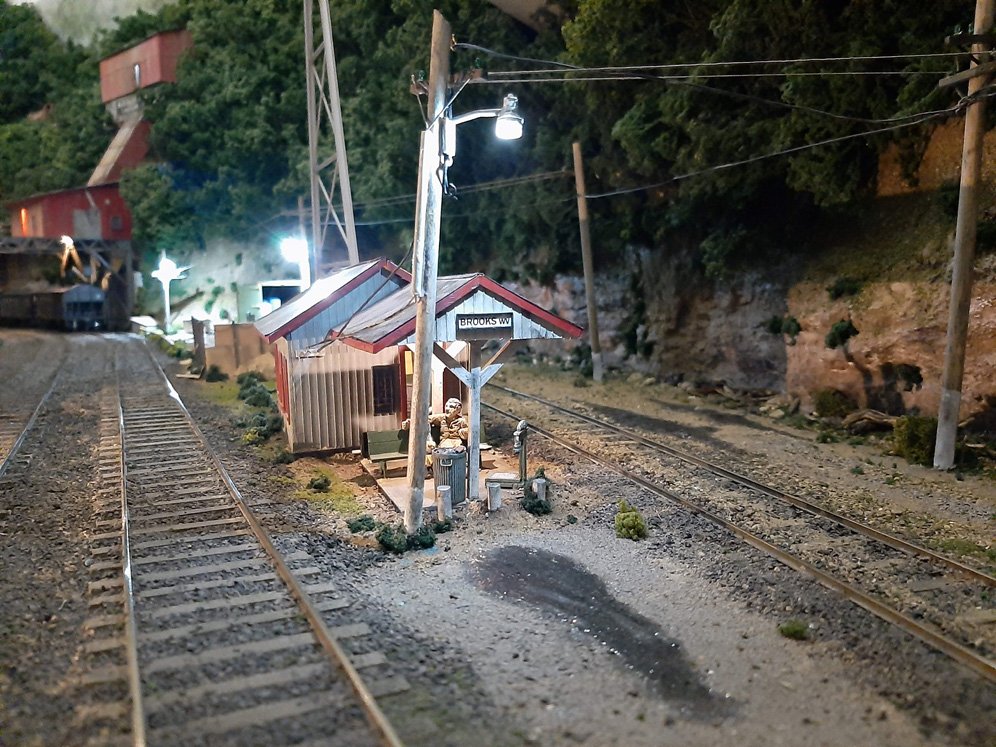
And some mud puddles.
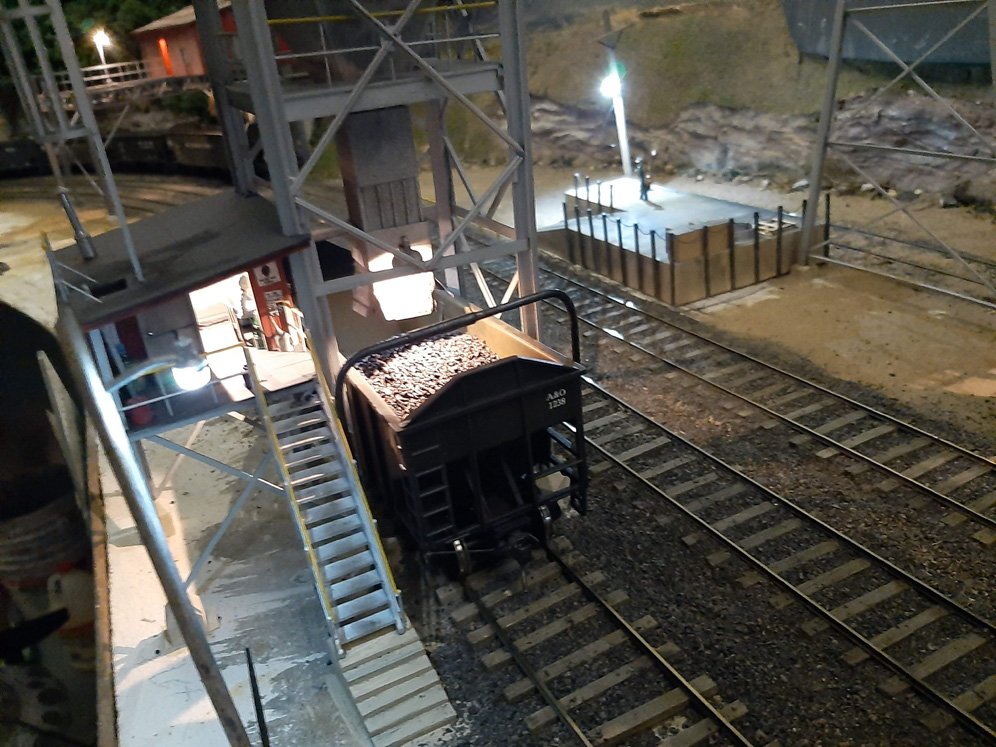
An embedded blackened brass rod protects the chute from anything but hoppers.
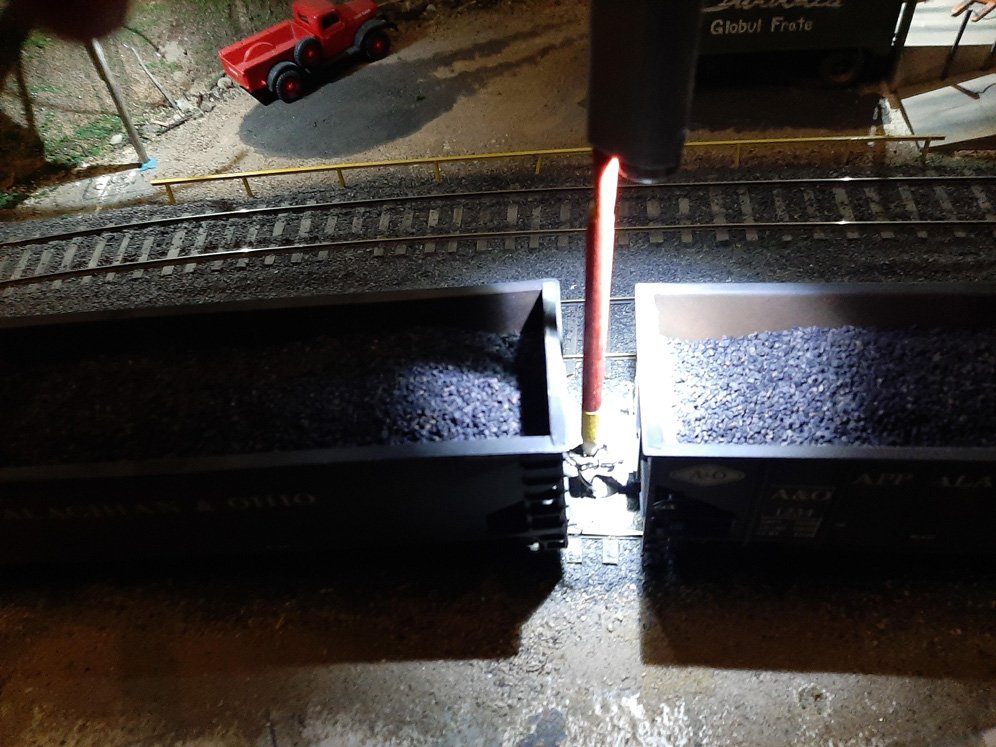
Uncoupling is this darkened scene is made easy with a penlight attached to a special A&O uncoupling tool.
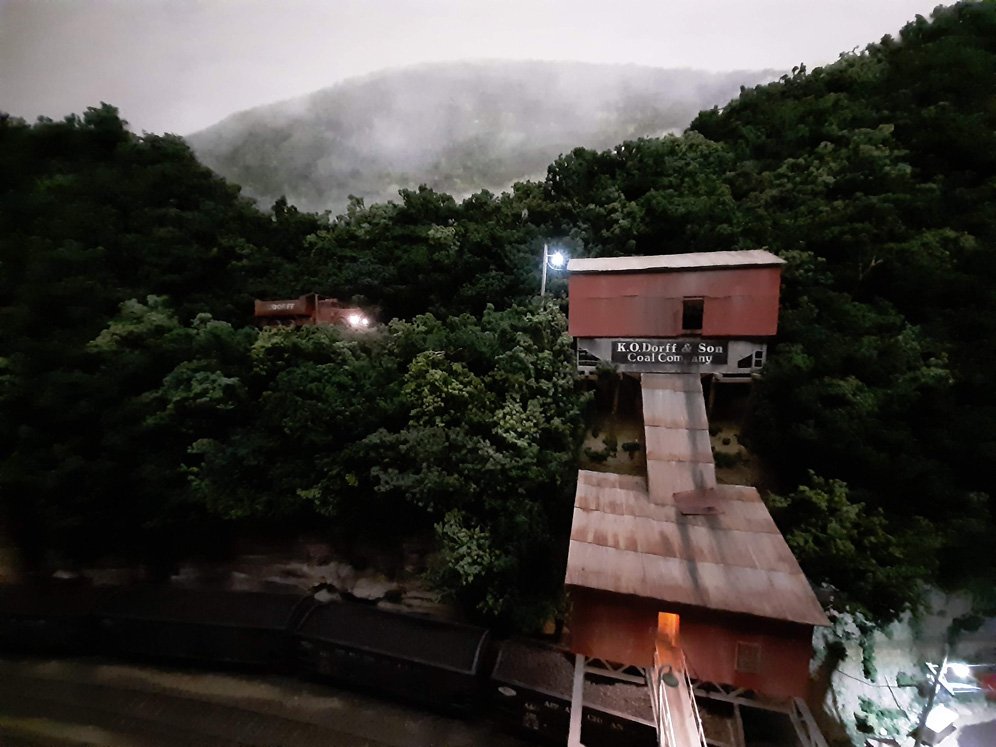
It only took three (!!!) tries to get the misty backdrop painting I desired.

The room lighting at Brooks is provided by a dimmable LED strip. The nod-under entrance into the Kayford Branch is at the constant thunderstorm town of Linnwood. Therefore the sound of distant thunder is always in the air. The storm that has moved down the Kayford valley has recently passed.

Mud puddles.
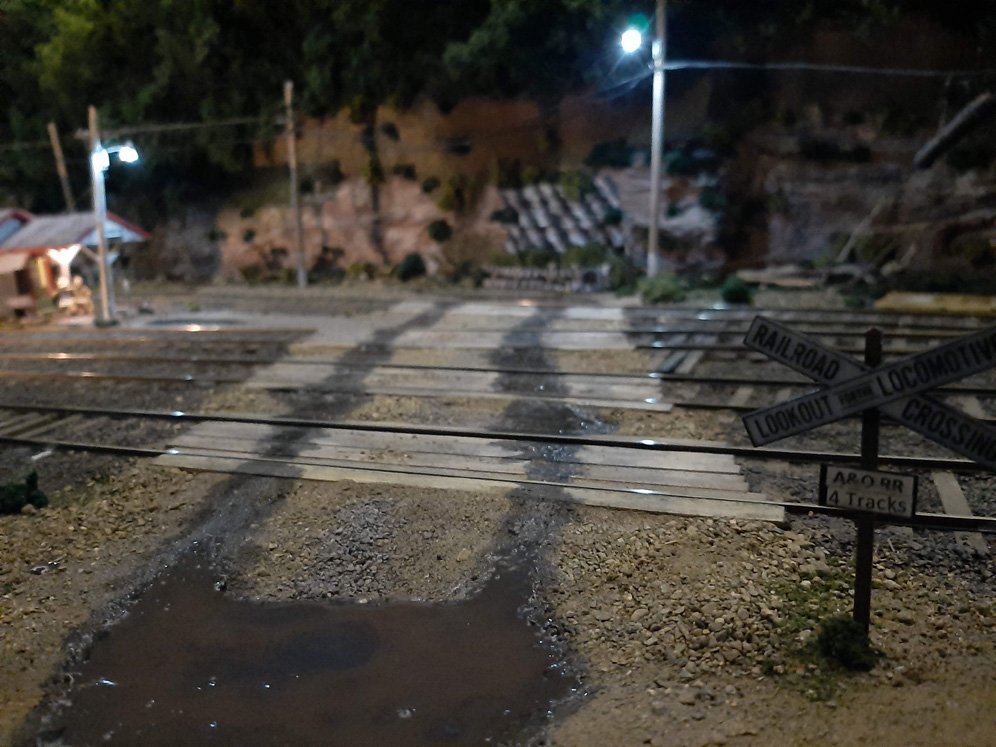
See the “Hawkins” Scene/Structure for how to do puddles.

The A&O version of the Clinchfield Coal Co. -” Brookstone”.
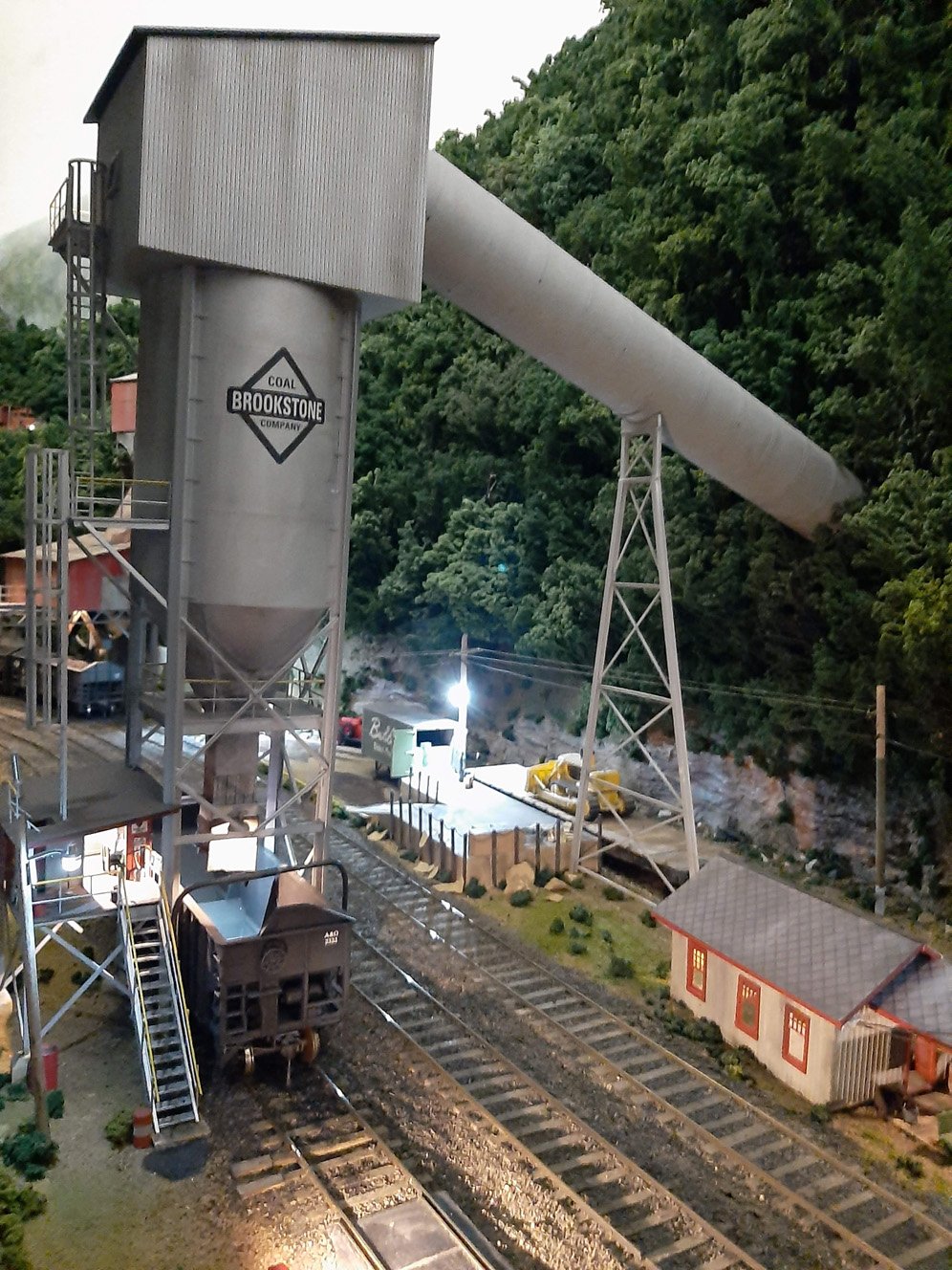
Another baby picture.
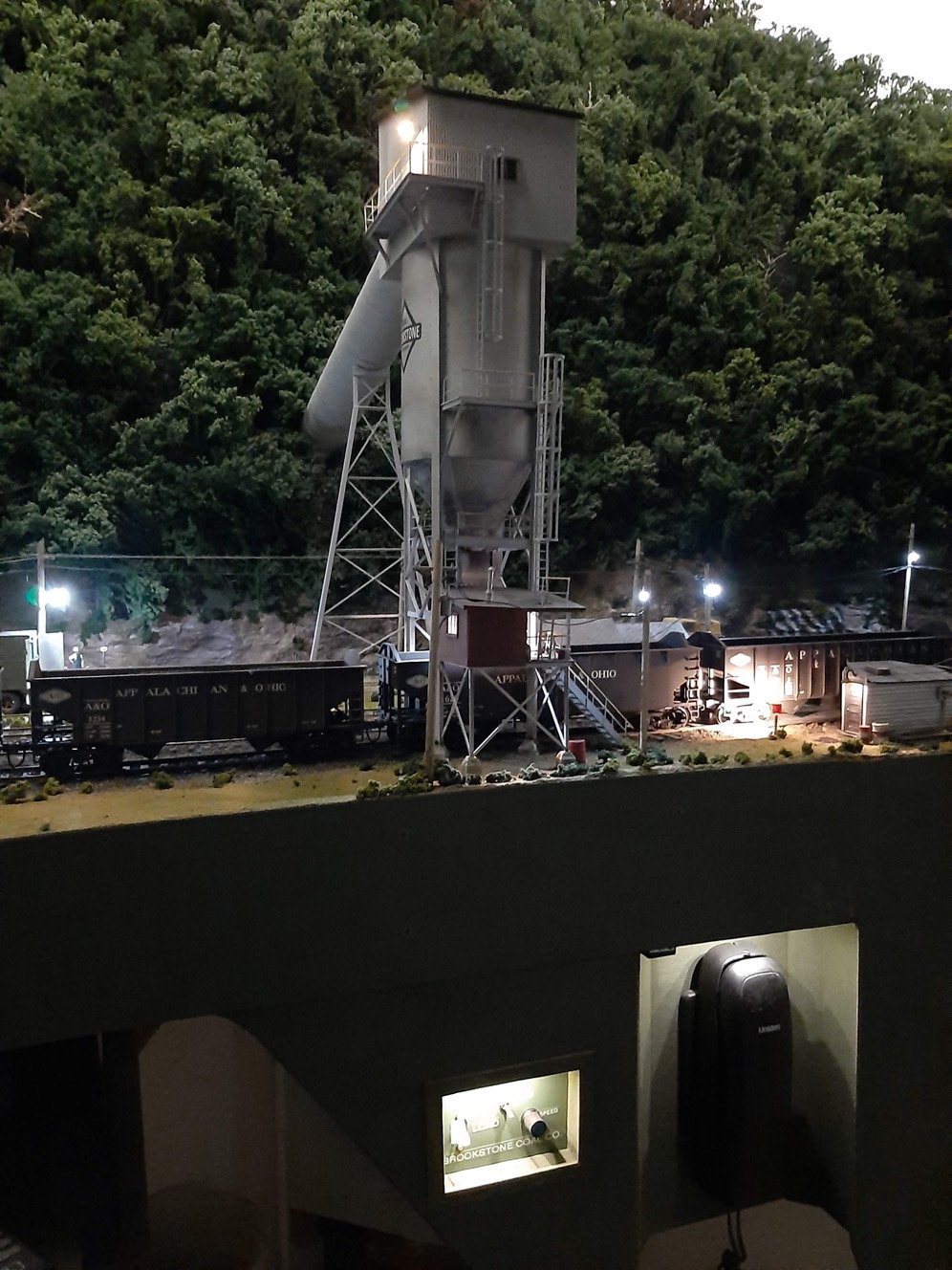
The controls for Brookstone are in view on the fascia. The conveyor belt speed can be adjusted to suit operator preference. And the DS telephone calls the town of Kayford, some 70 angled feet away and the midpoint on the branch.

A bird’s eye view of Brooks as completed minus hillside town, unseen here, but to the far left. Compare to the first two pictures of this all-to-narrow/shallow scene :)
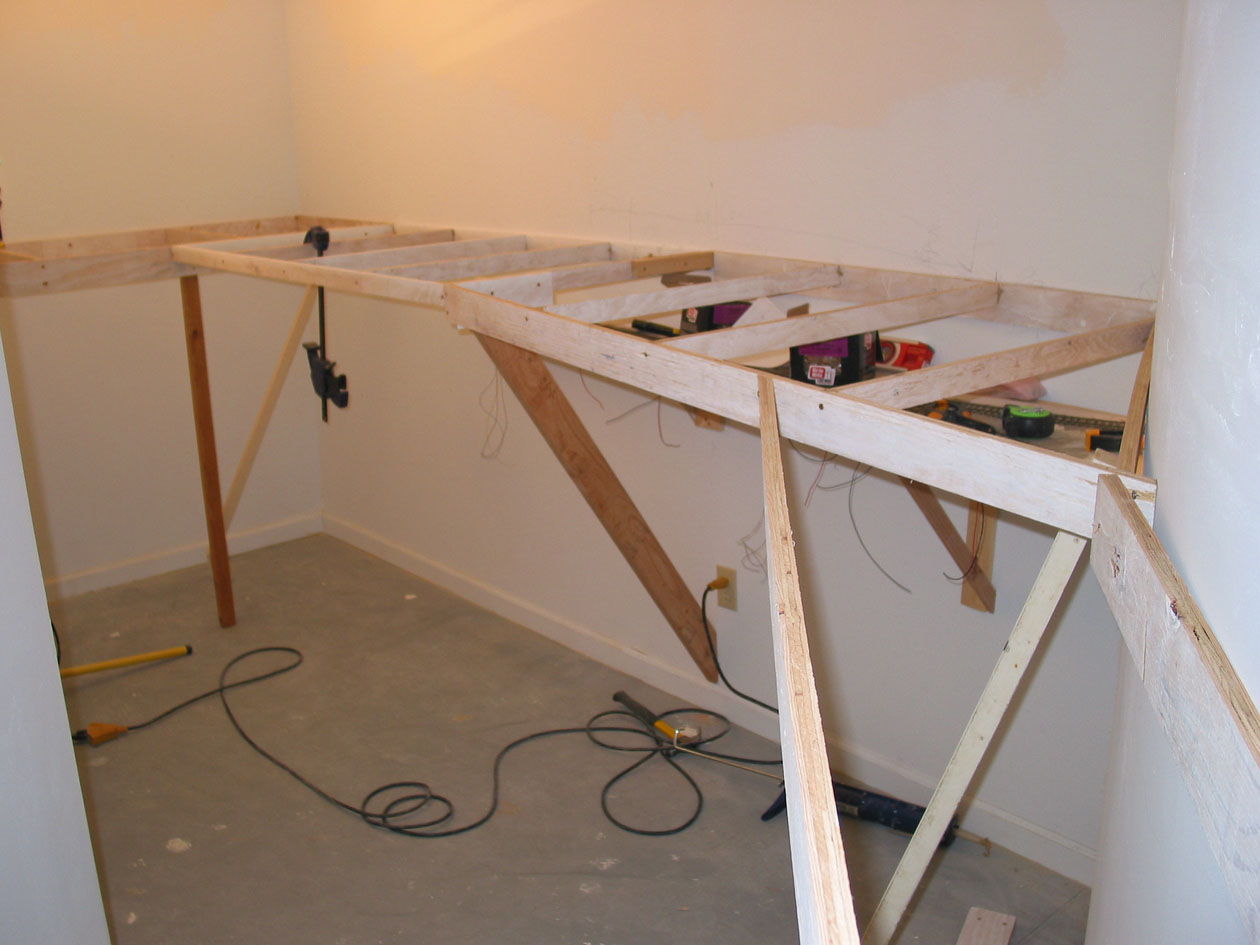
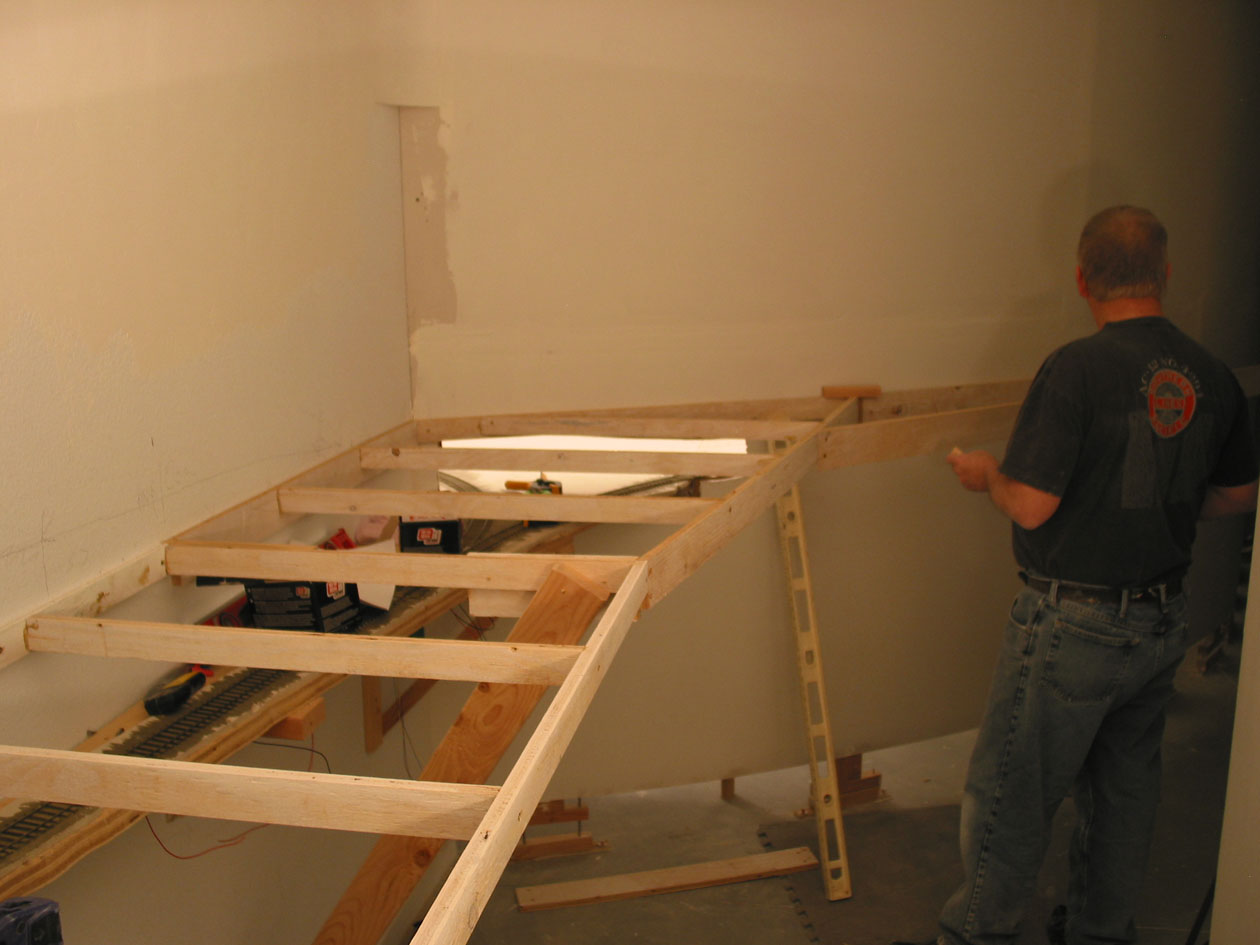
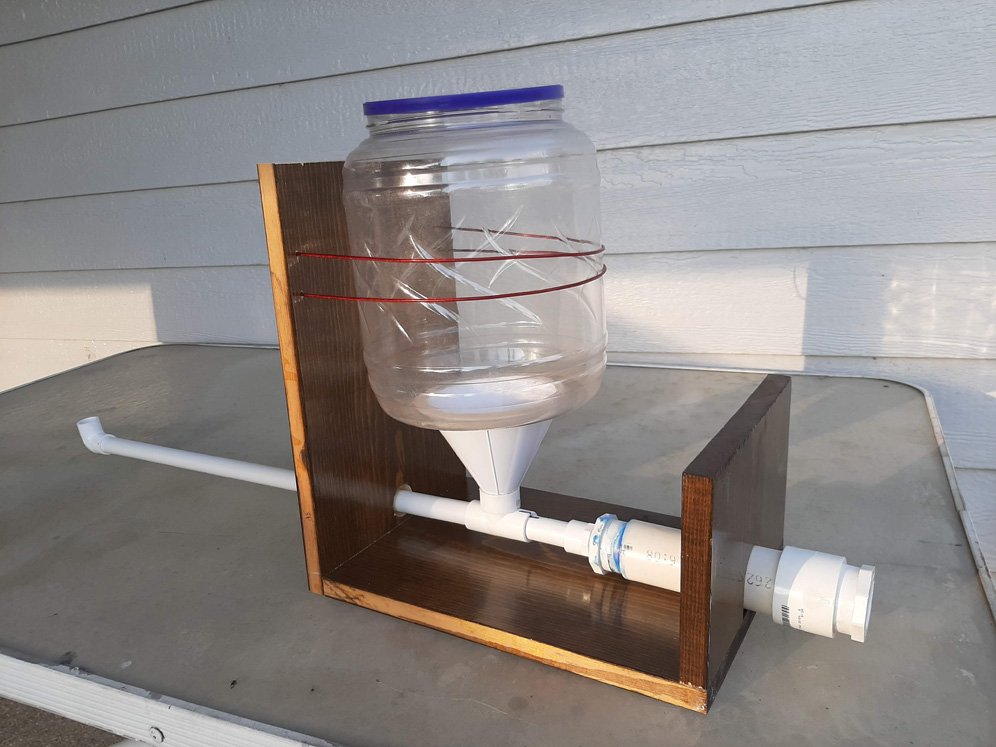




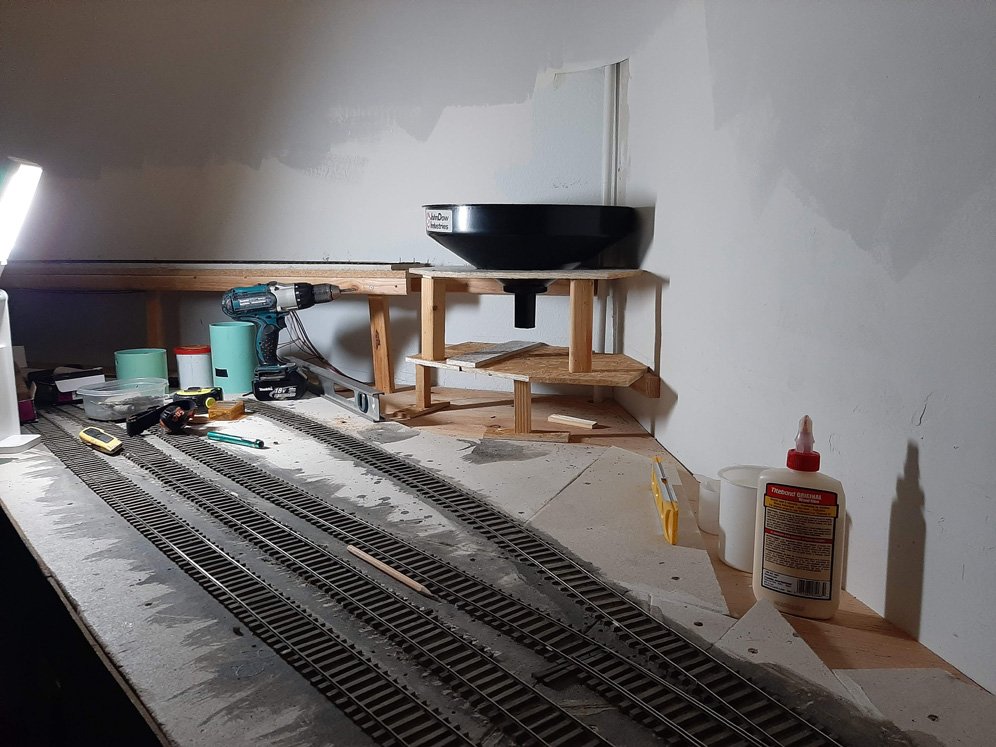

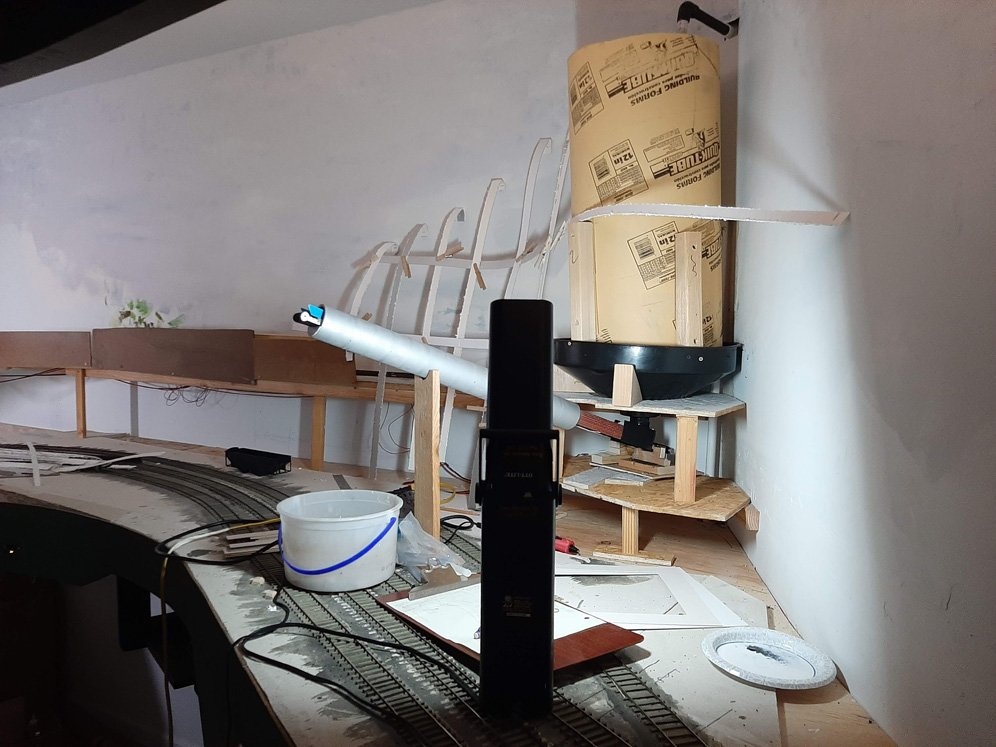



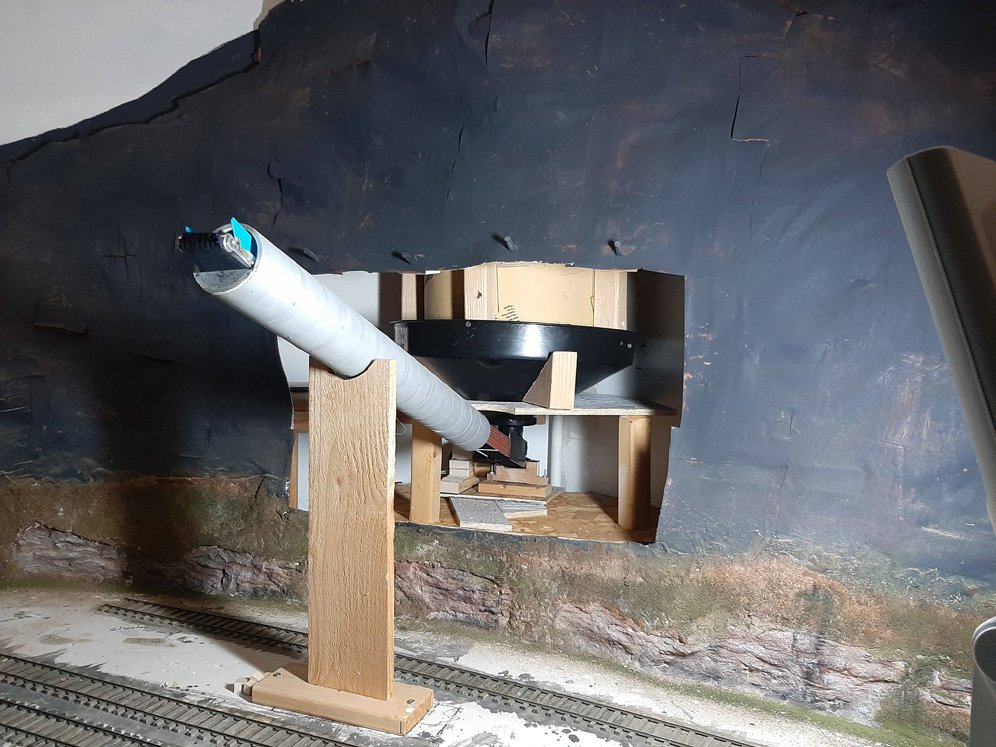
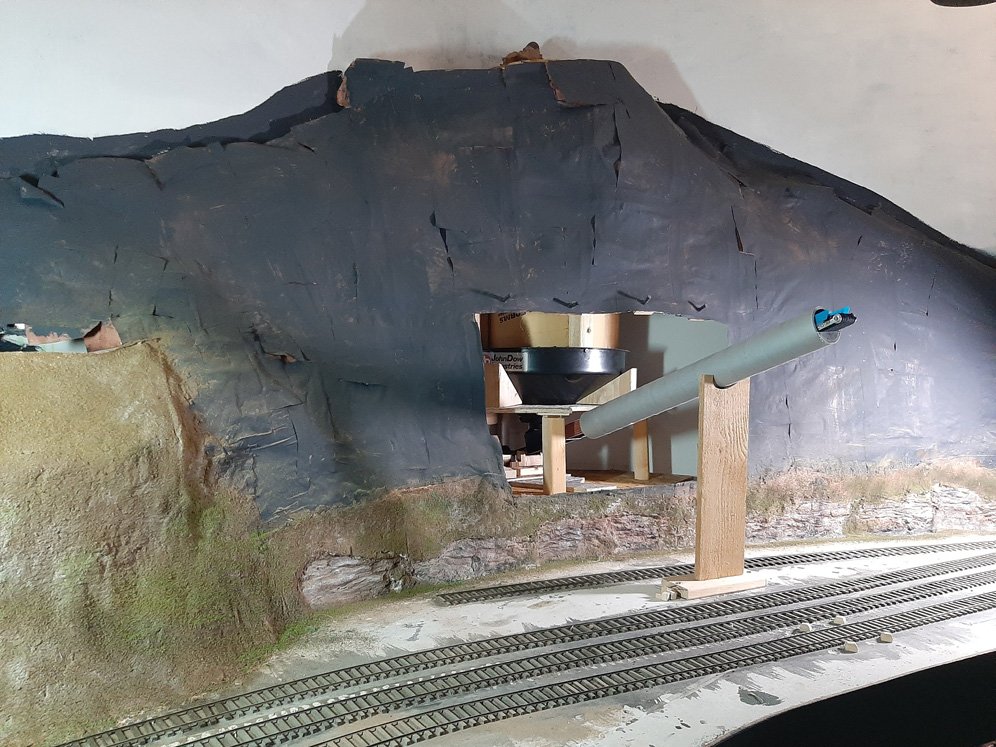
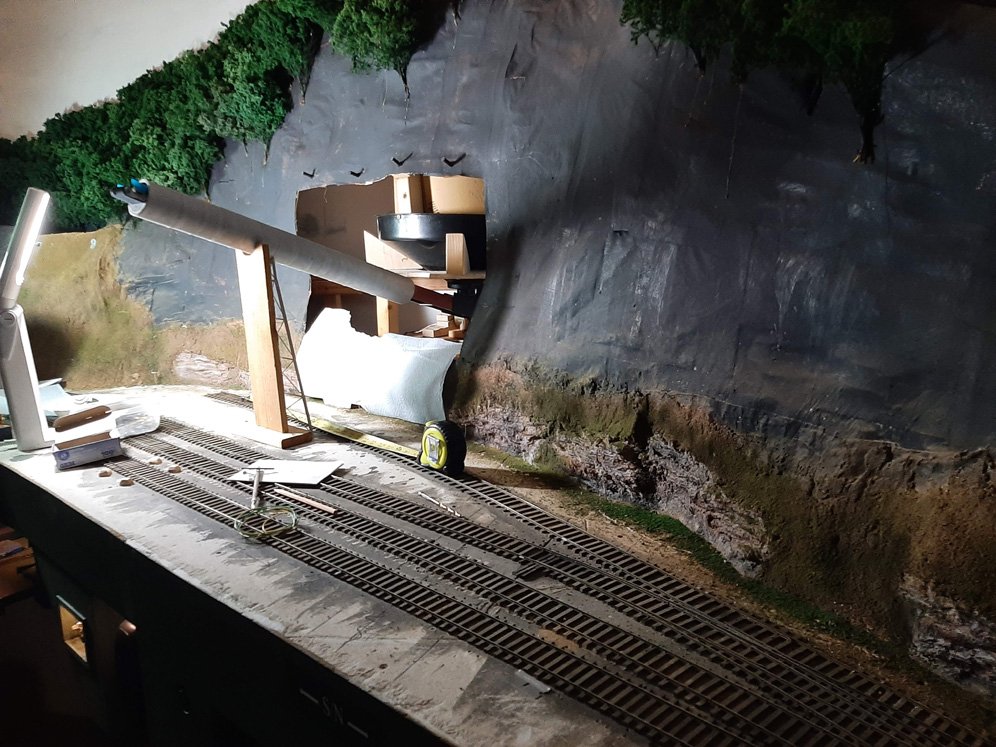
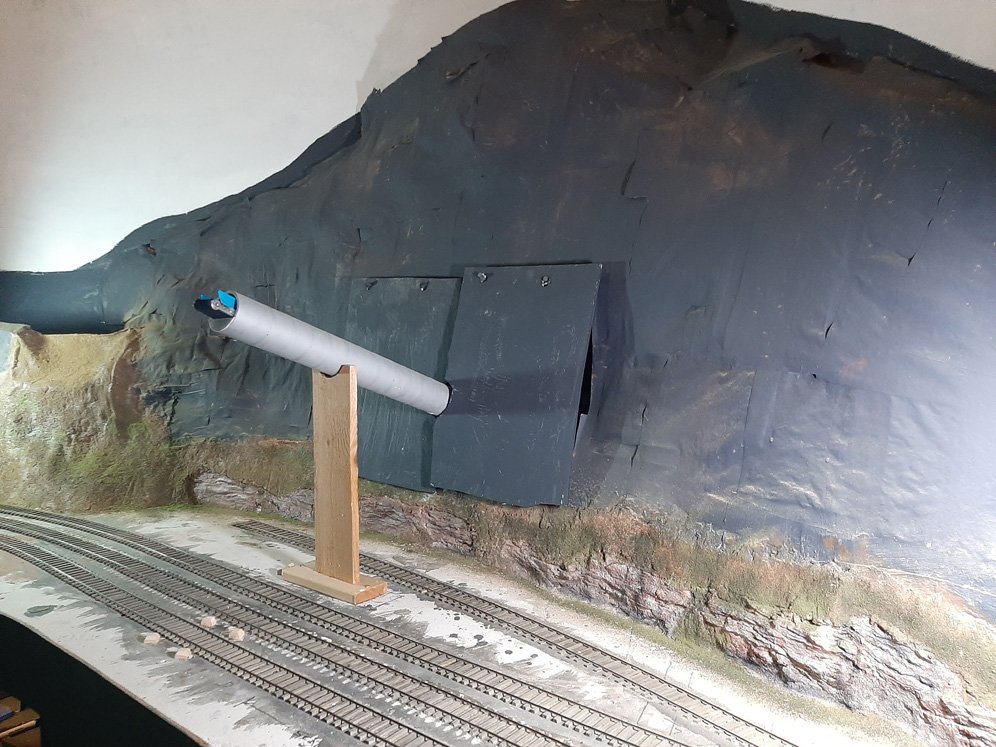
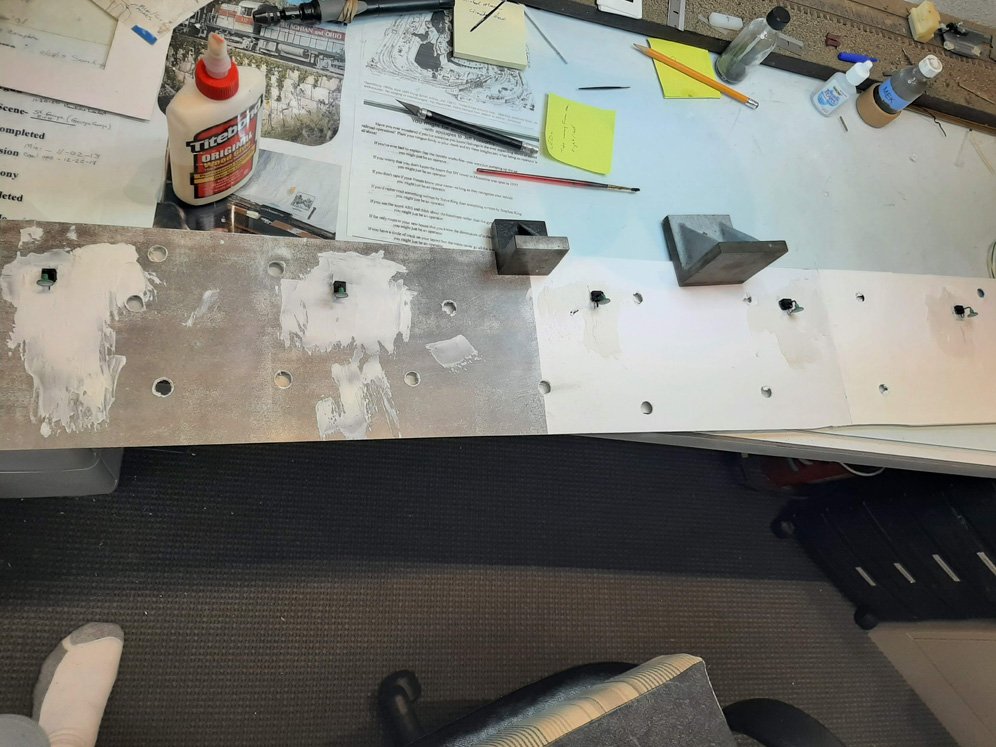
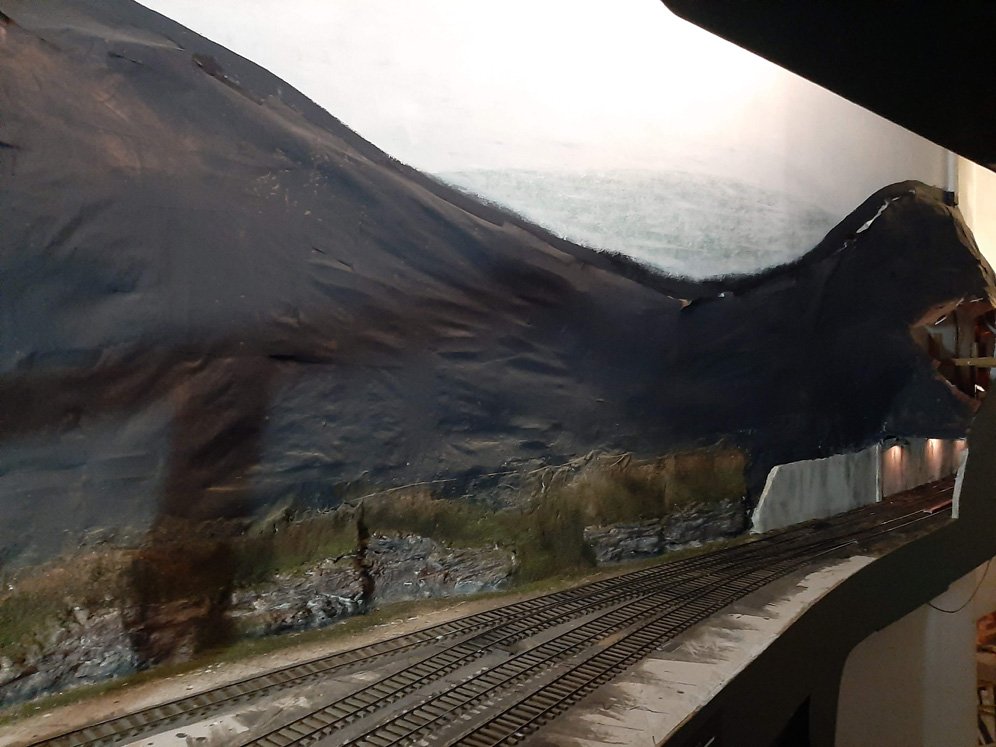
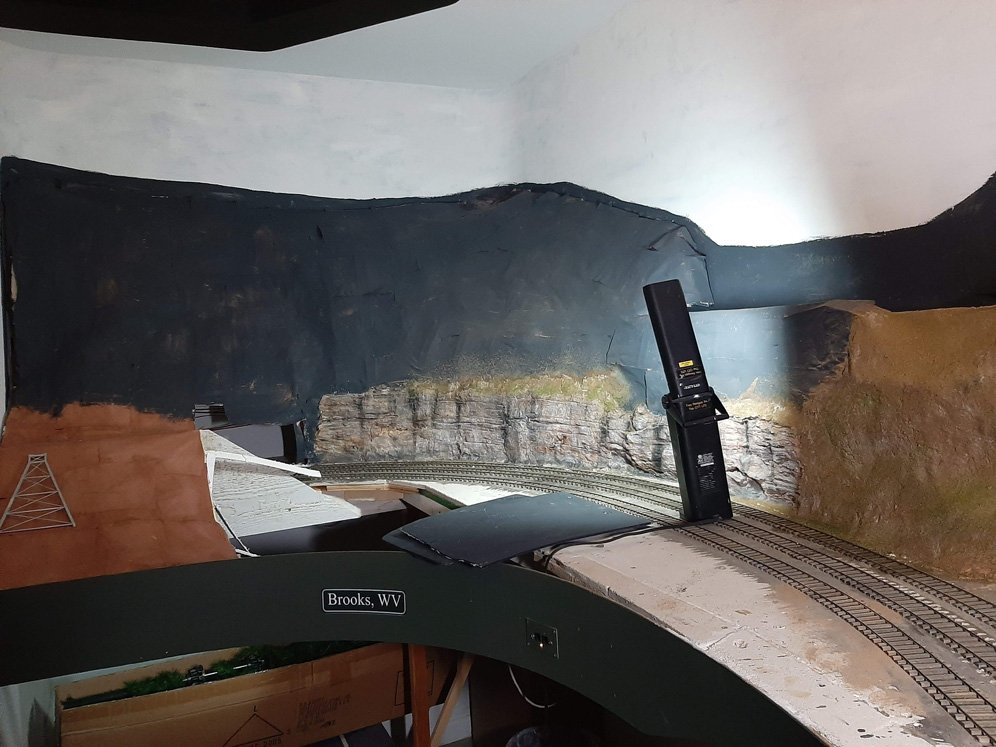

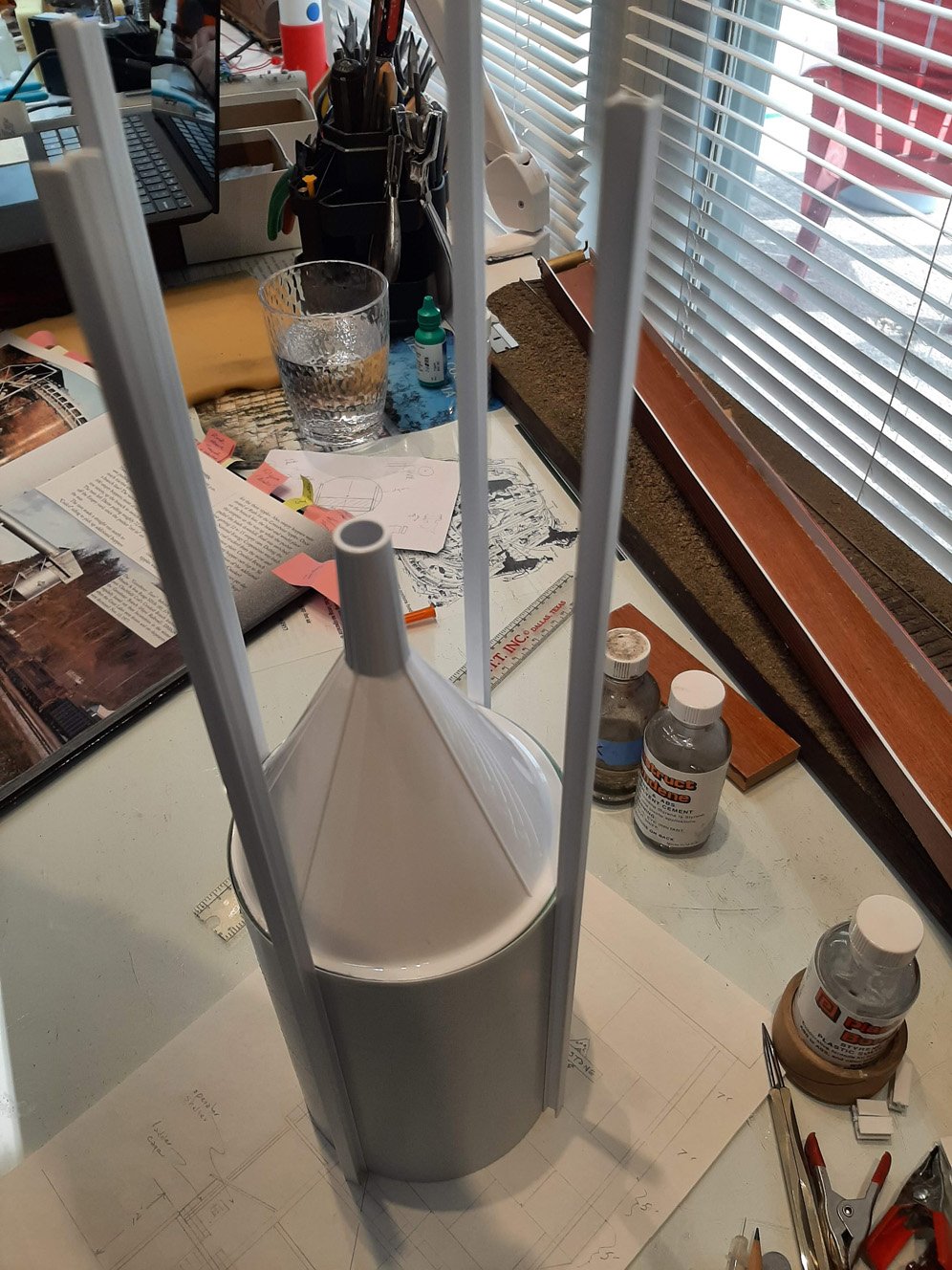
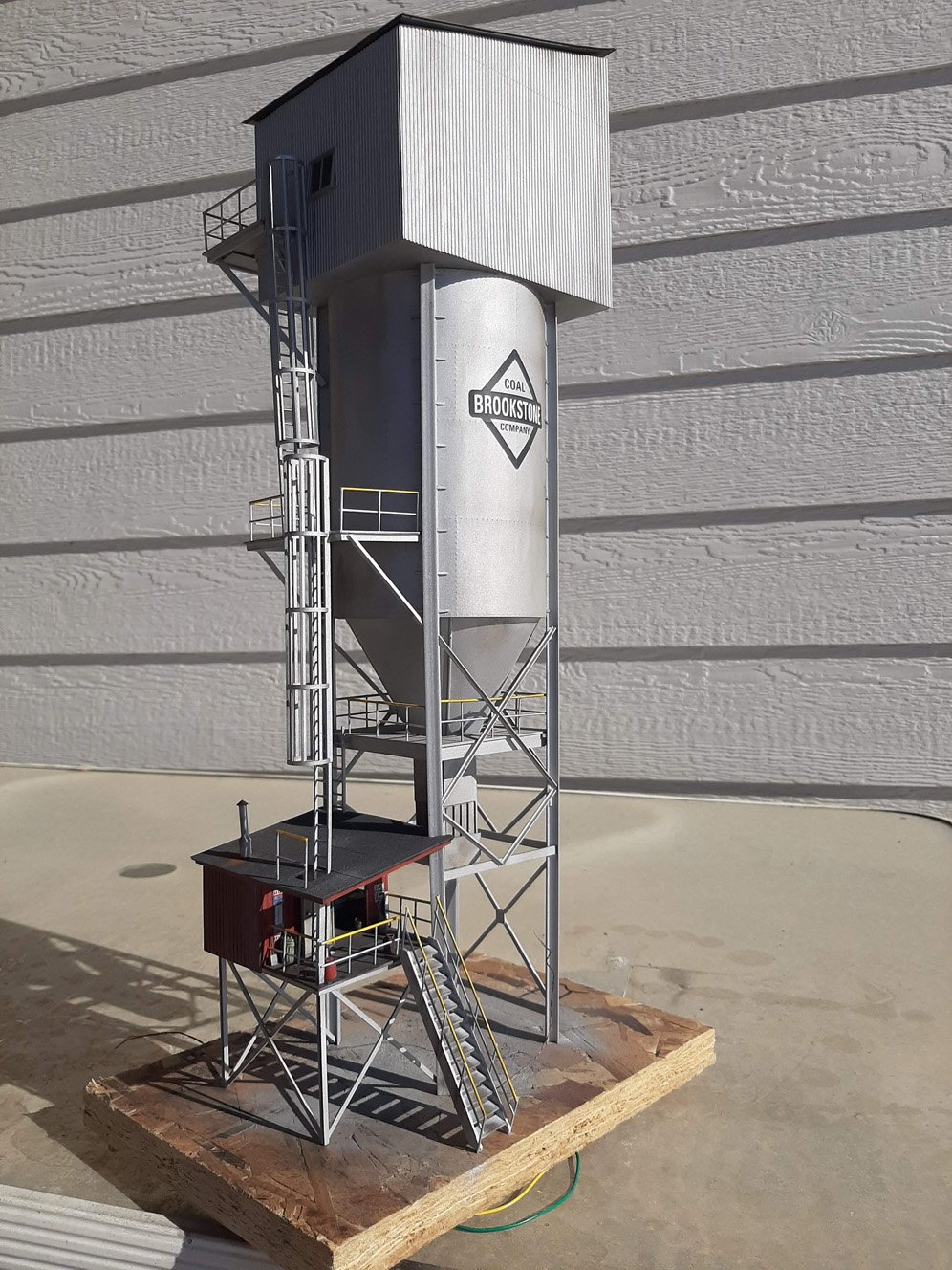

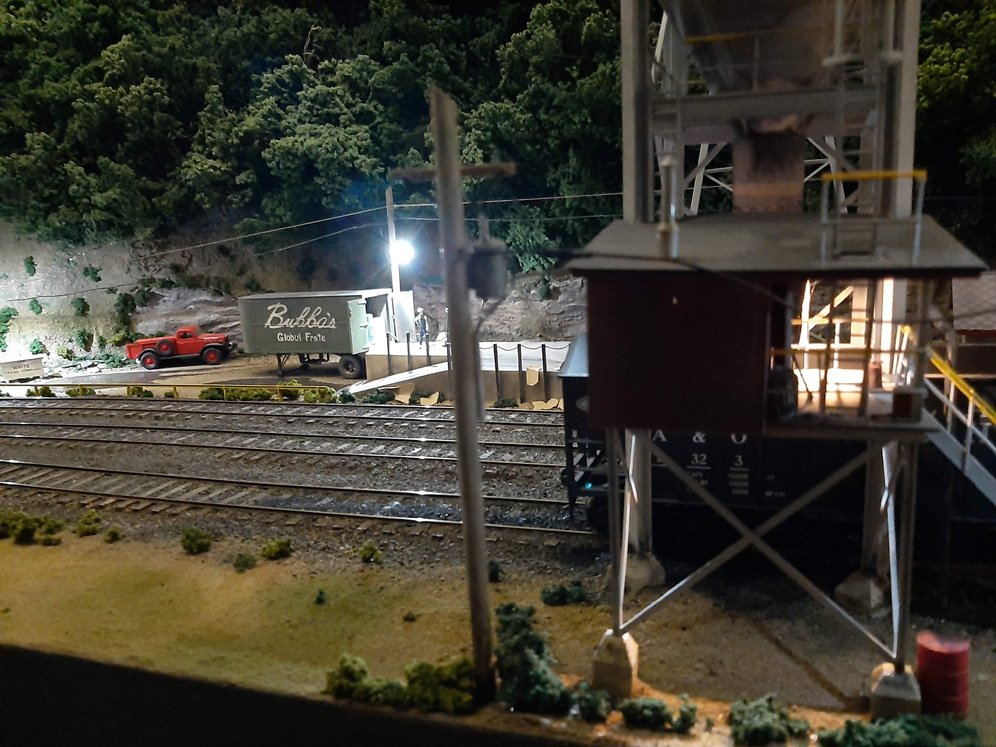

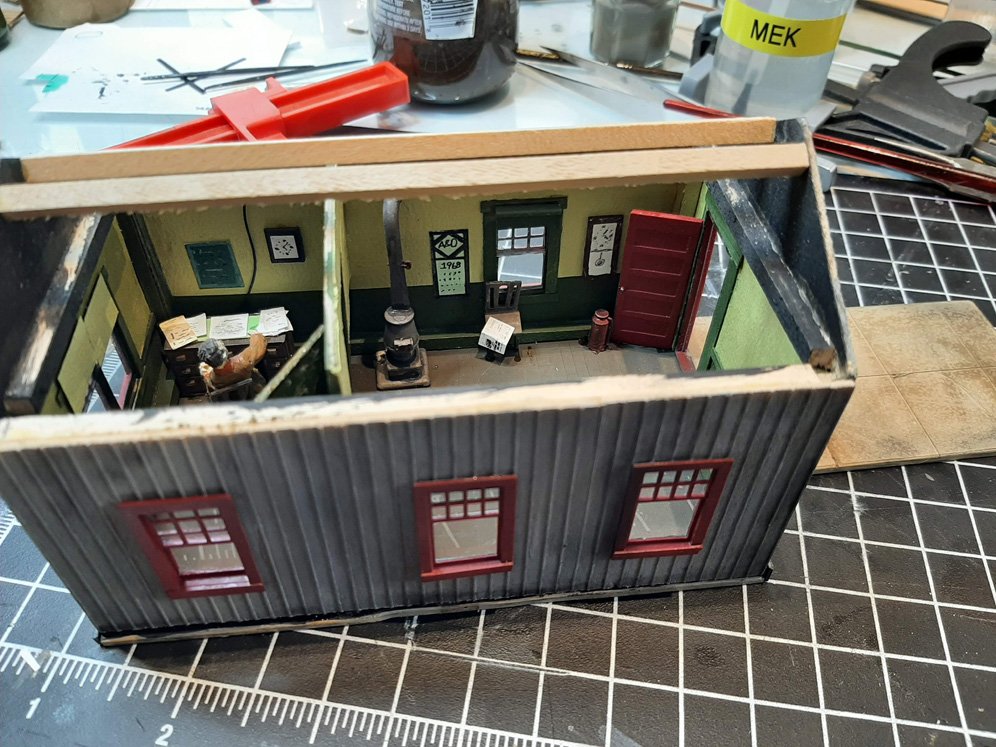
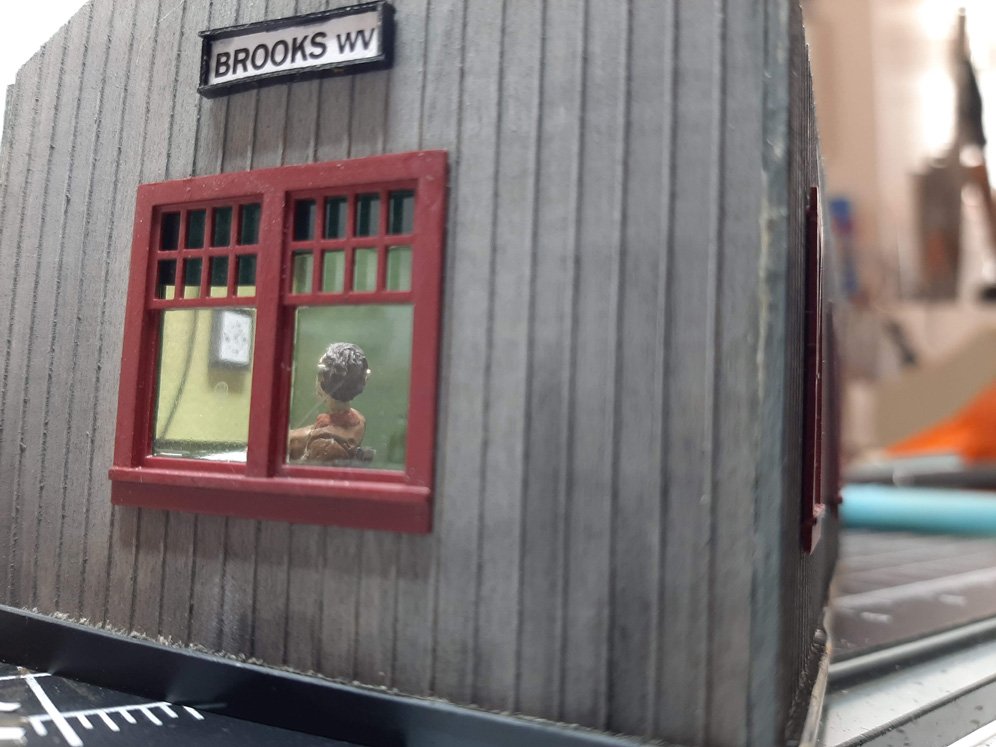
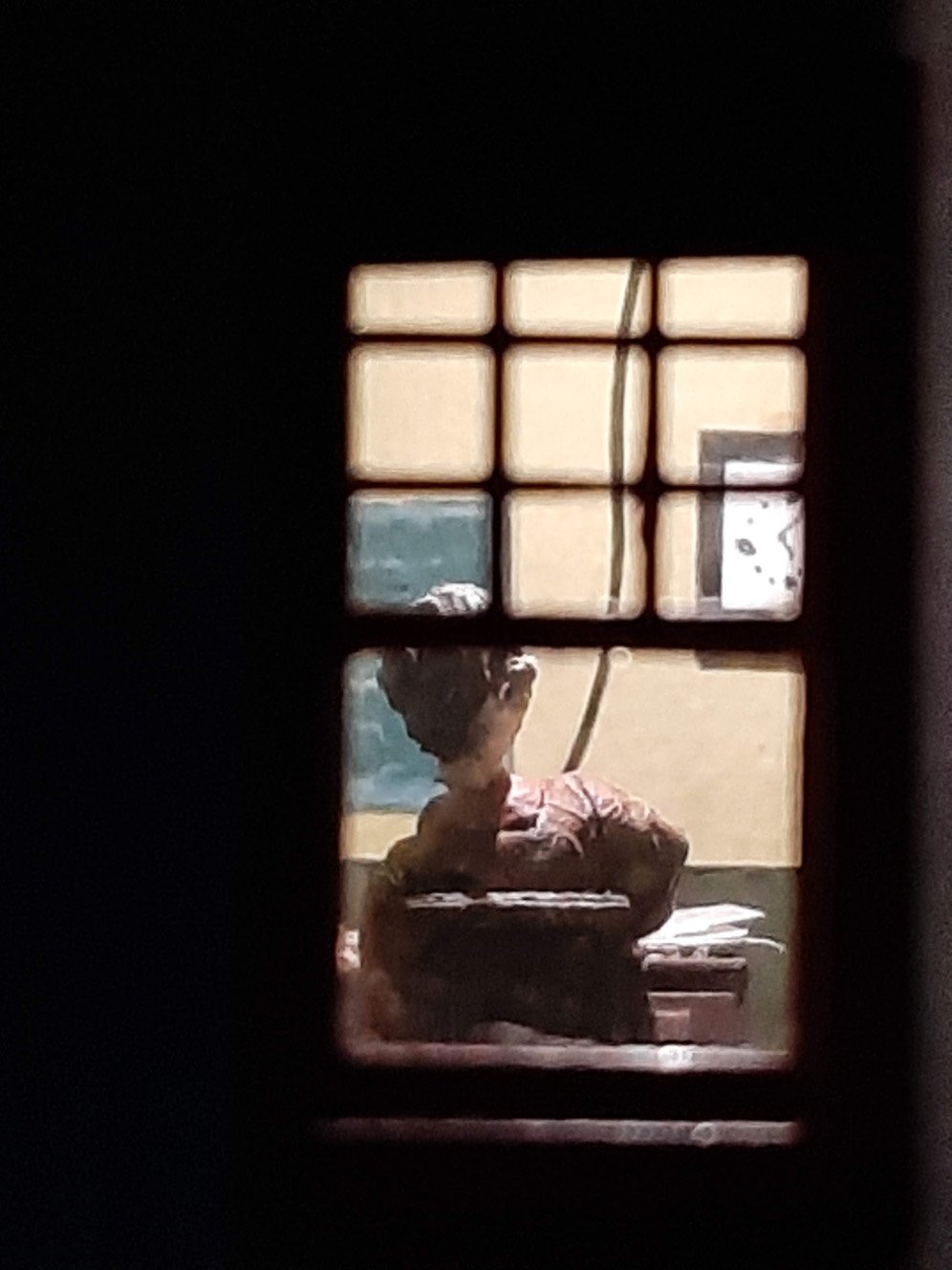
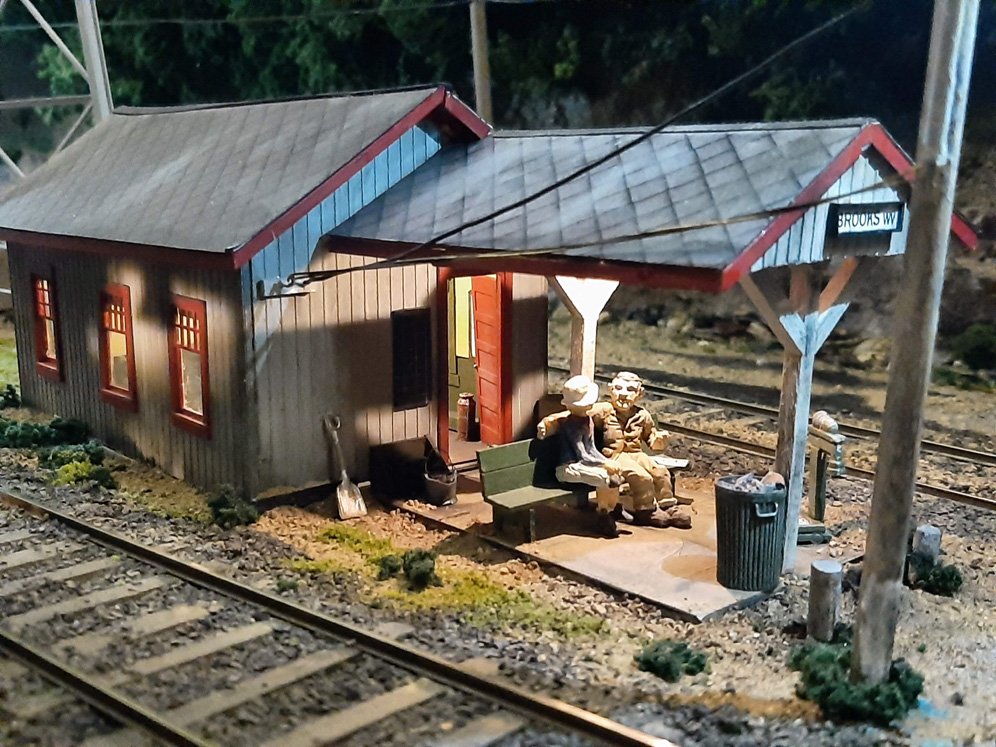

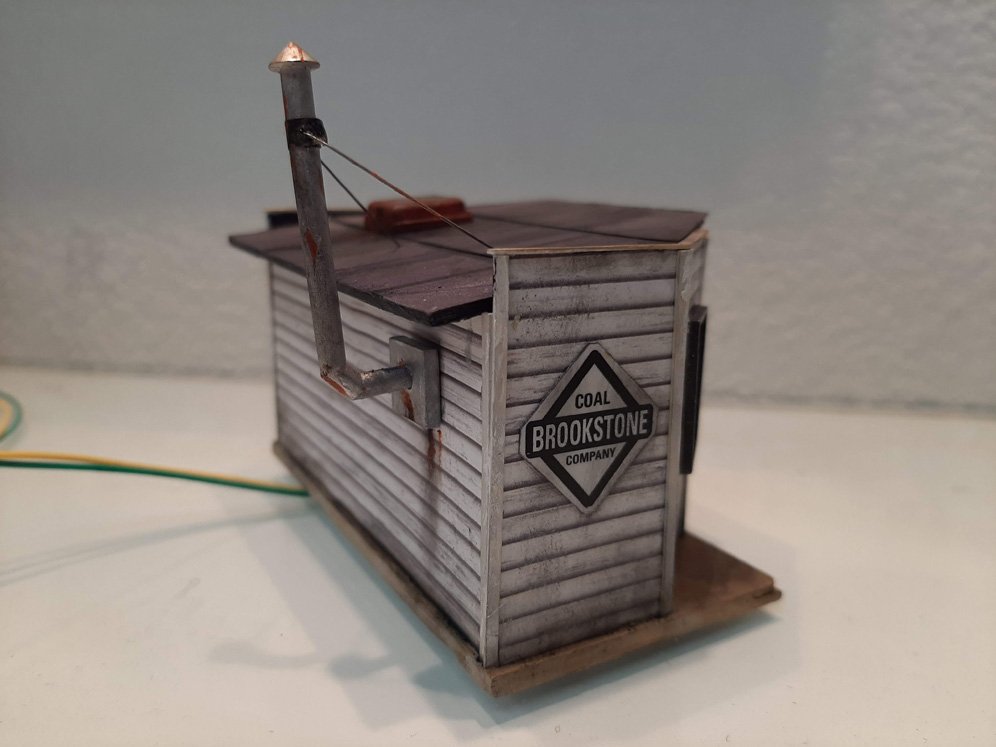

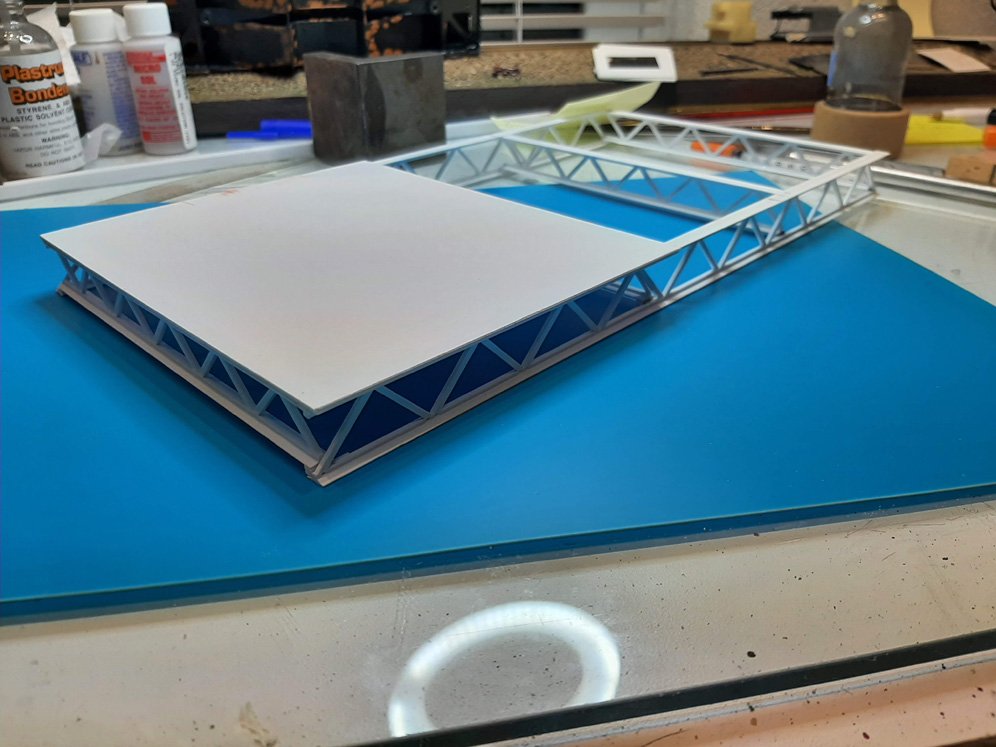
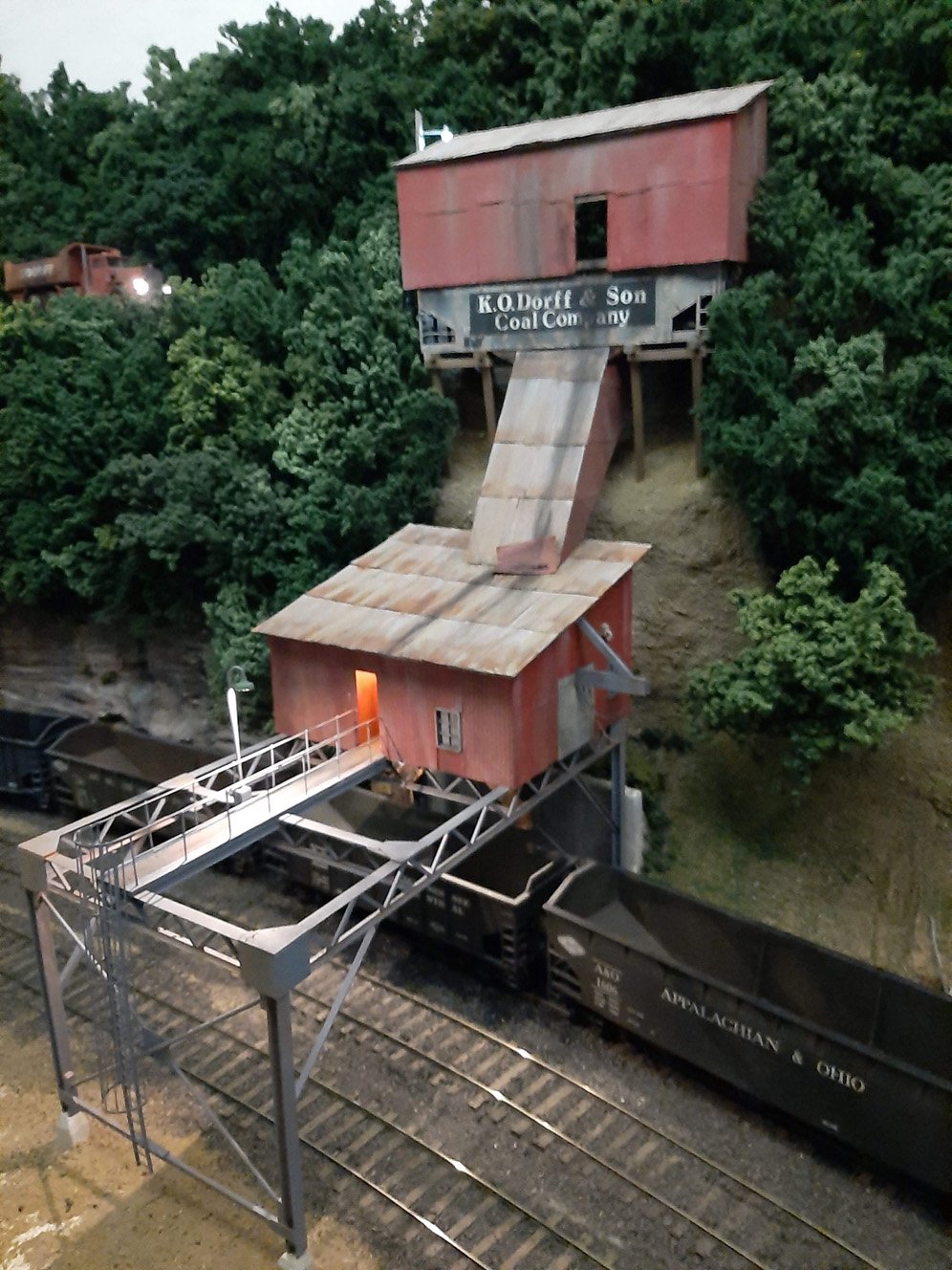
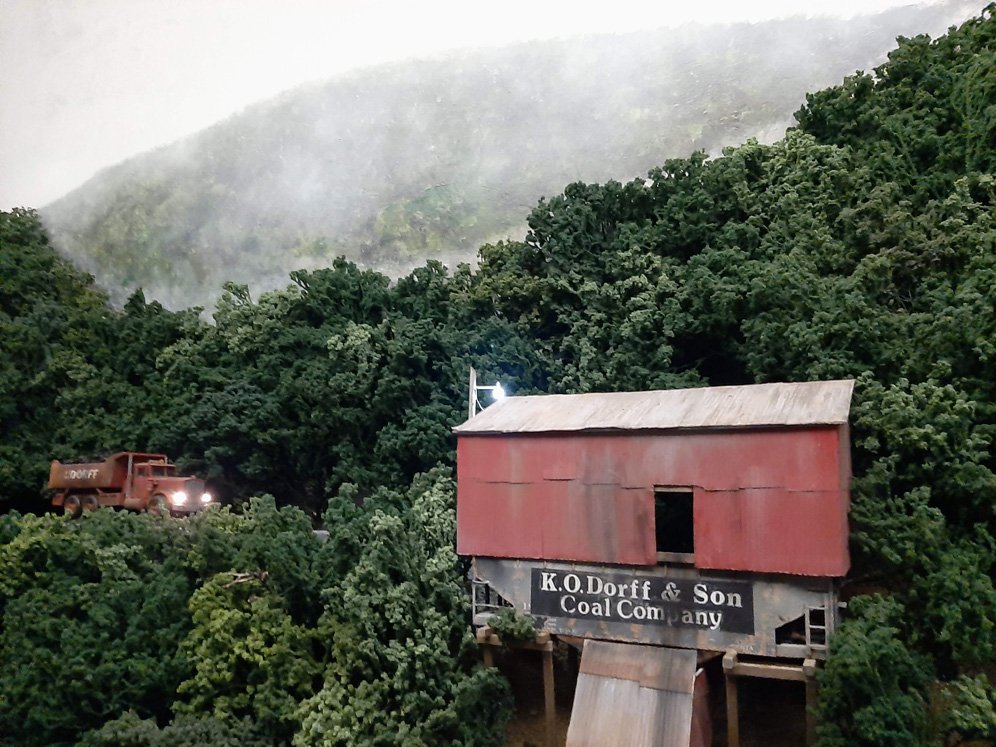
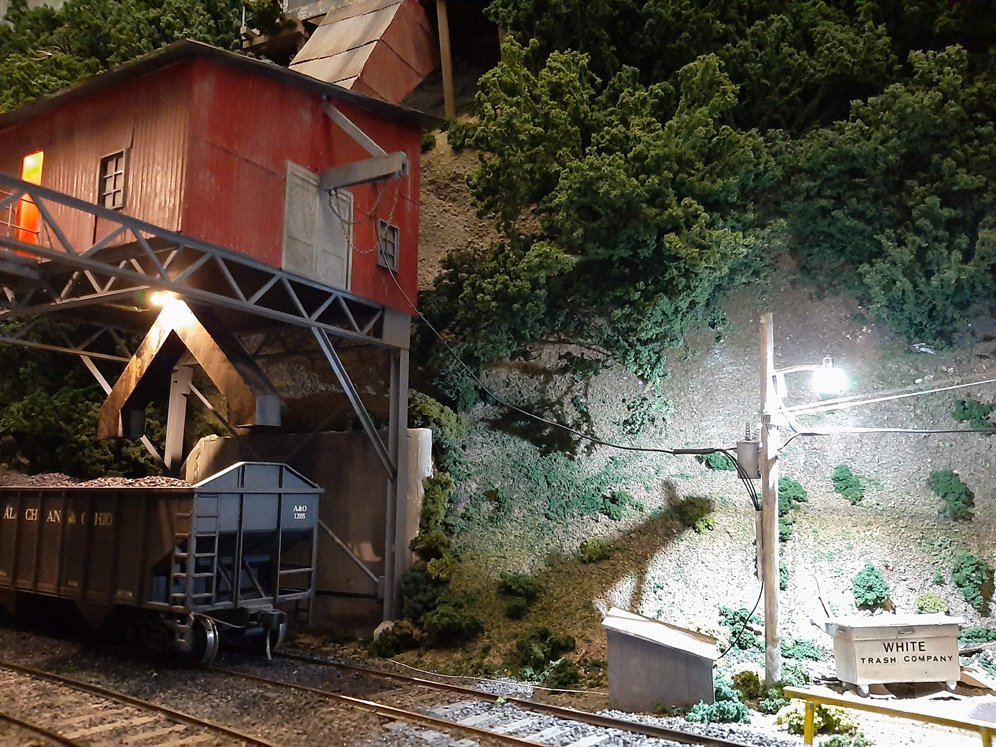




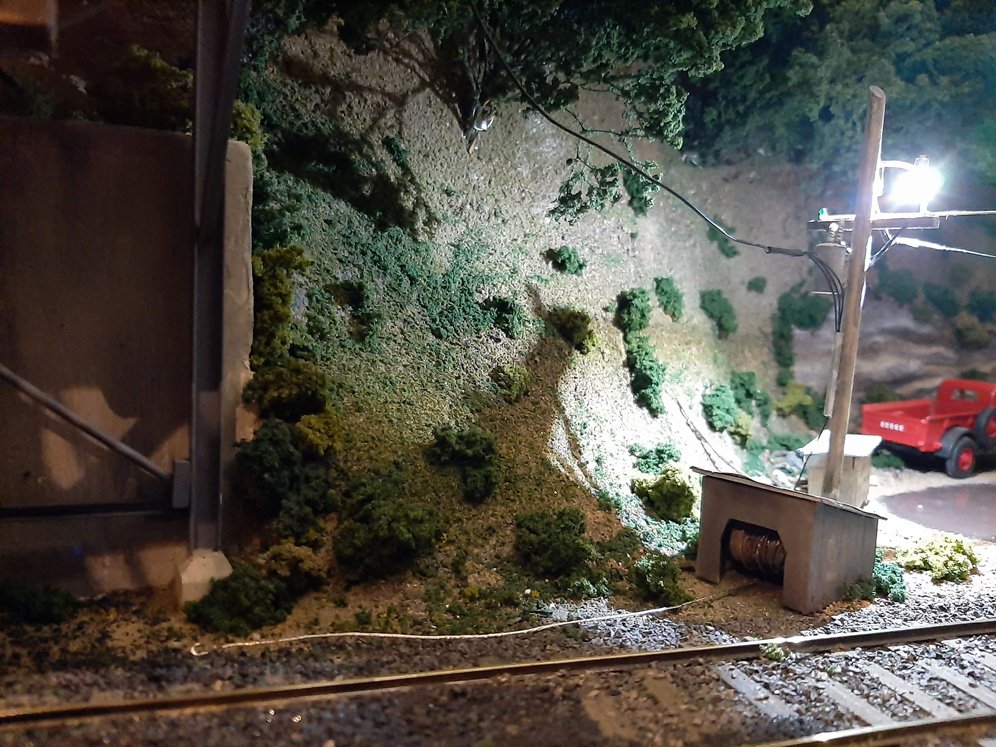

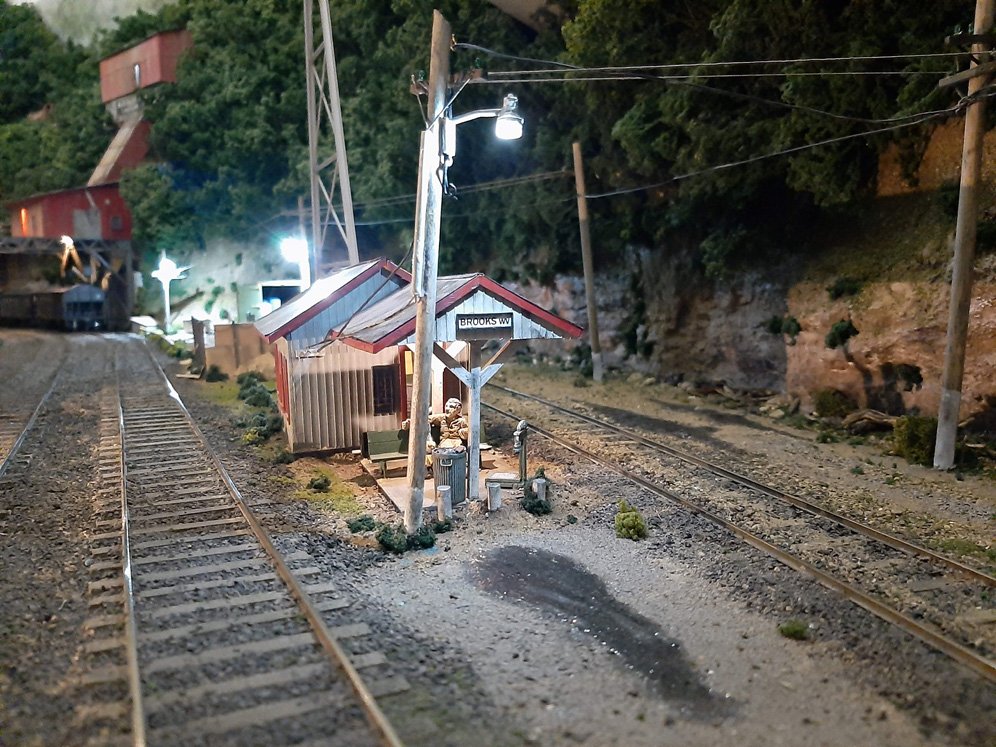
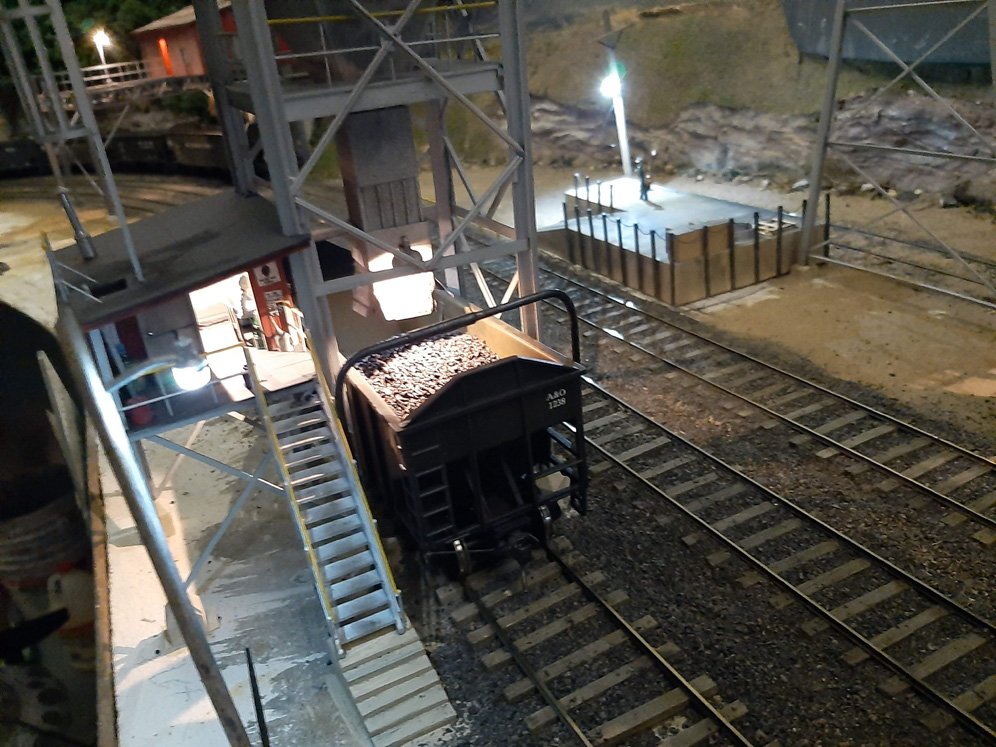
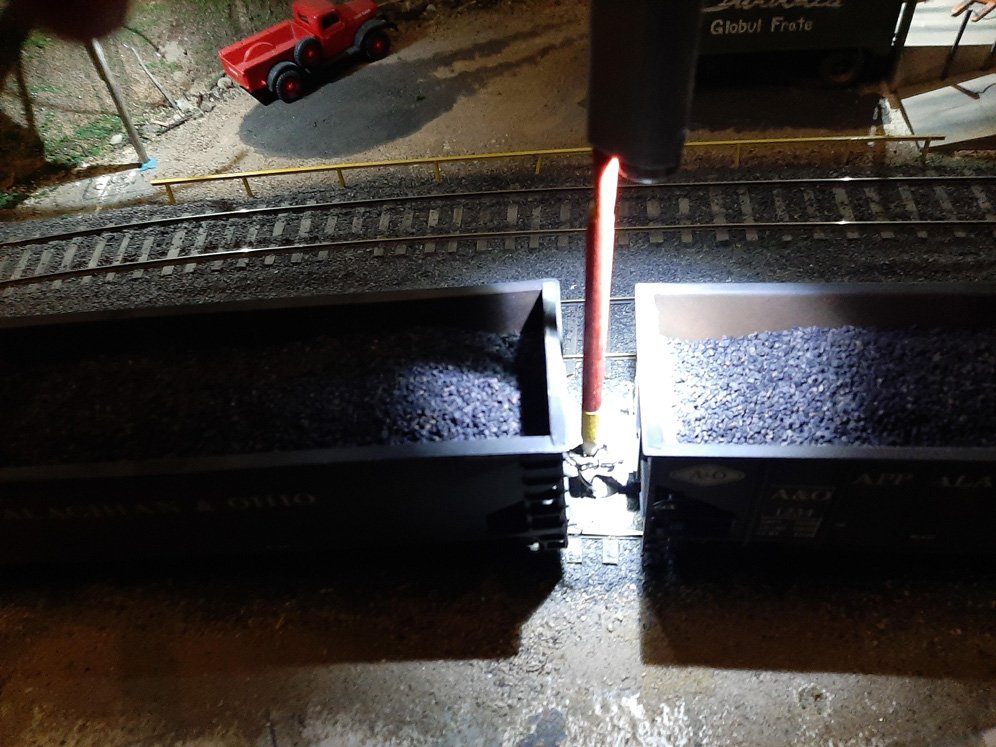
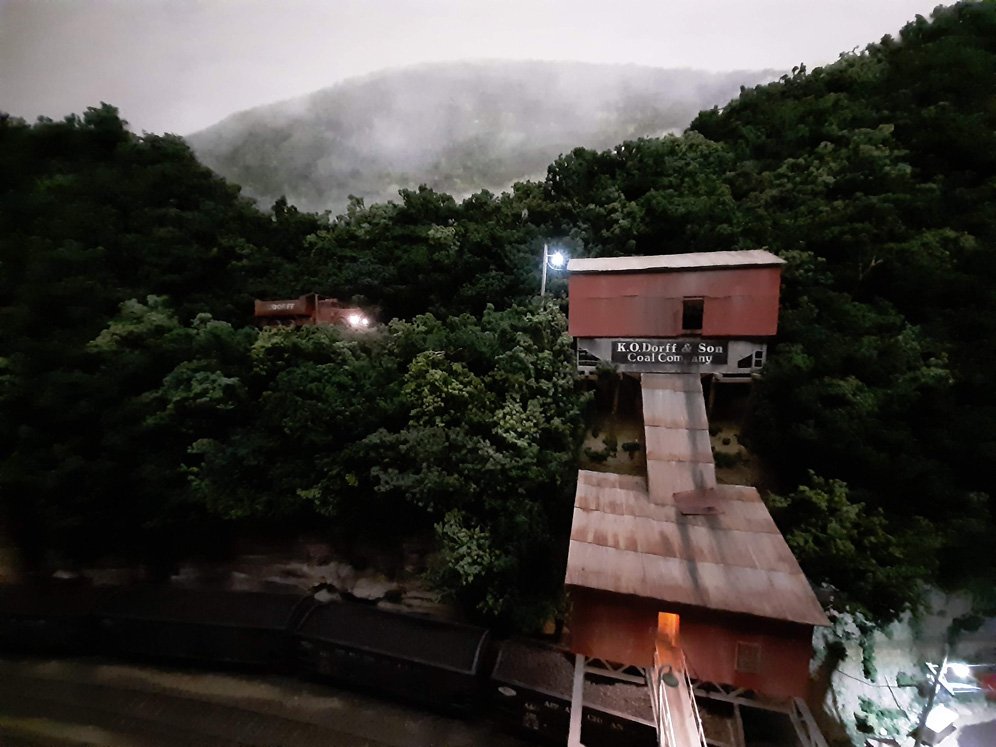


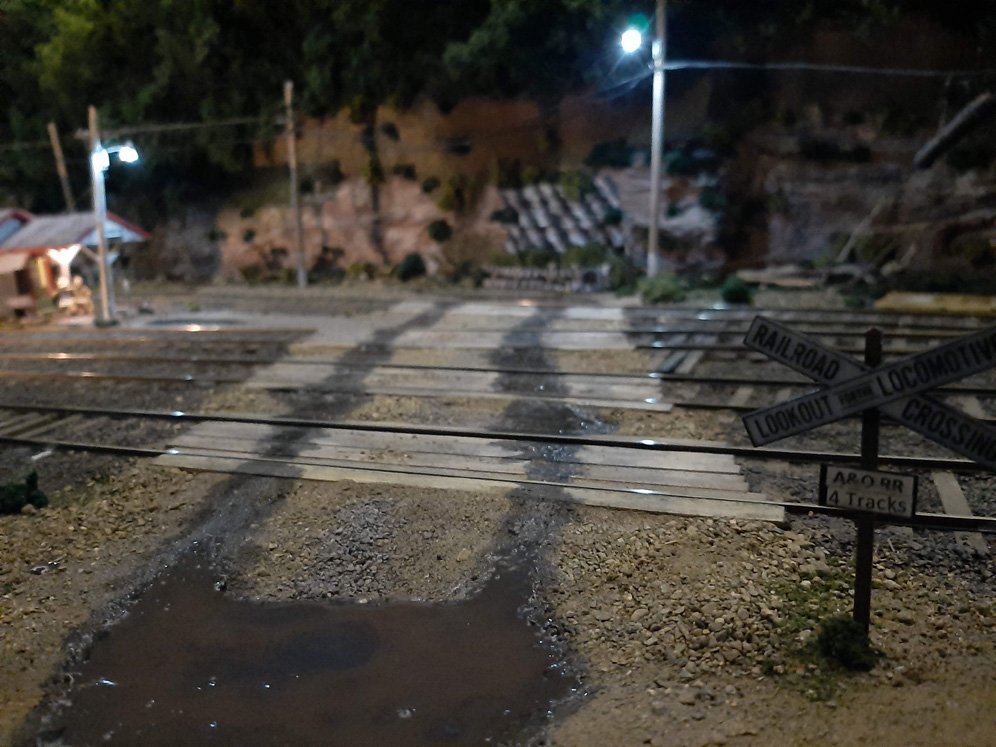

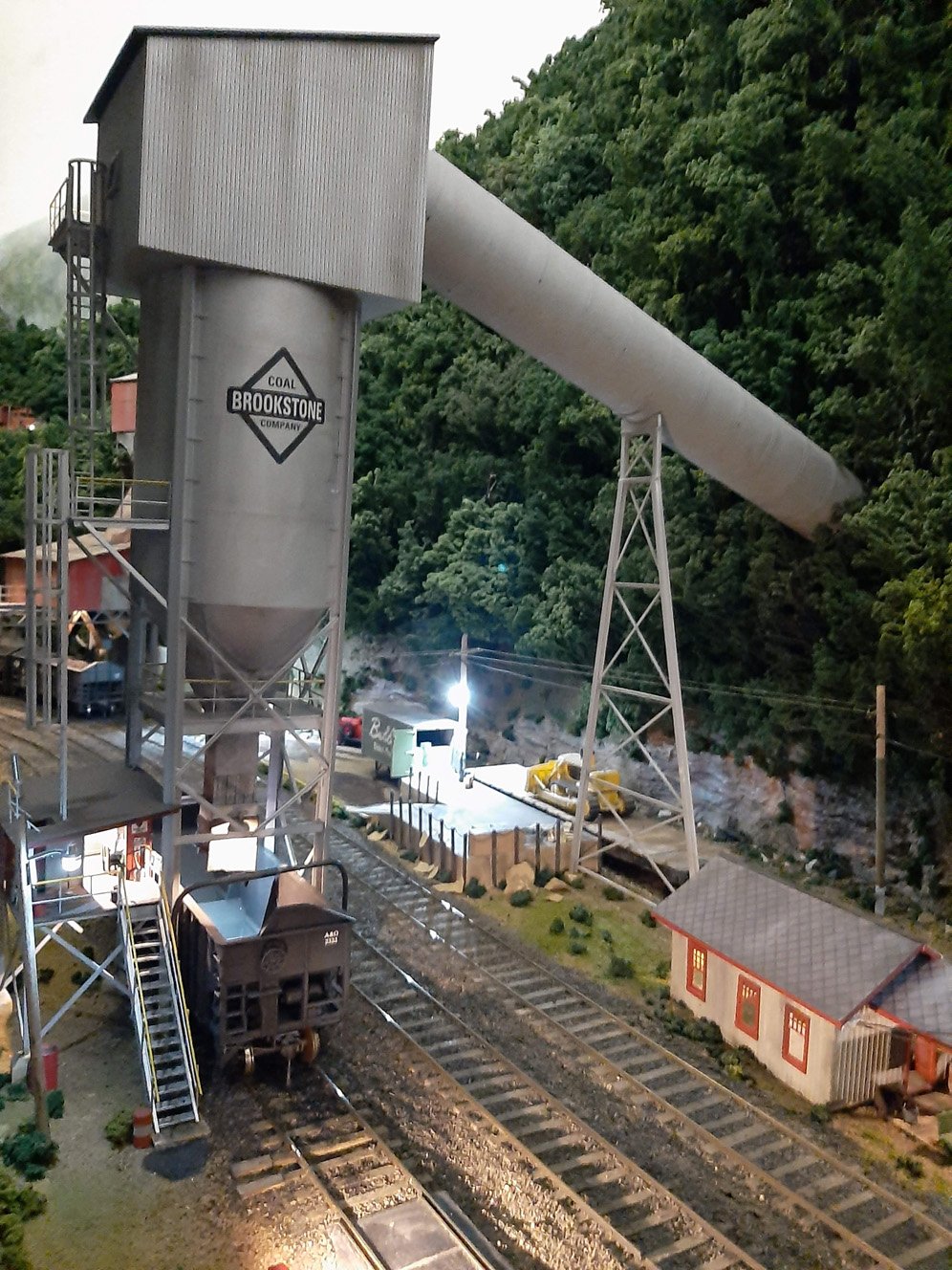
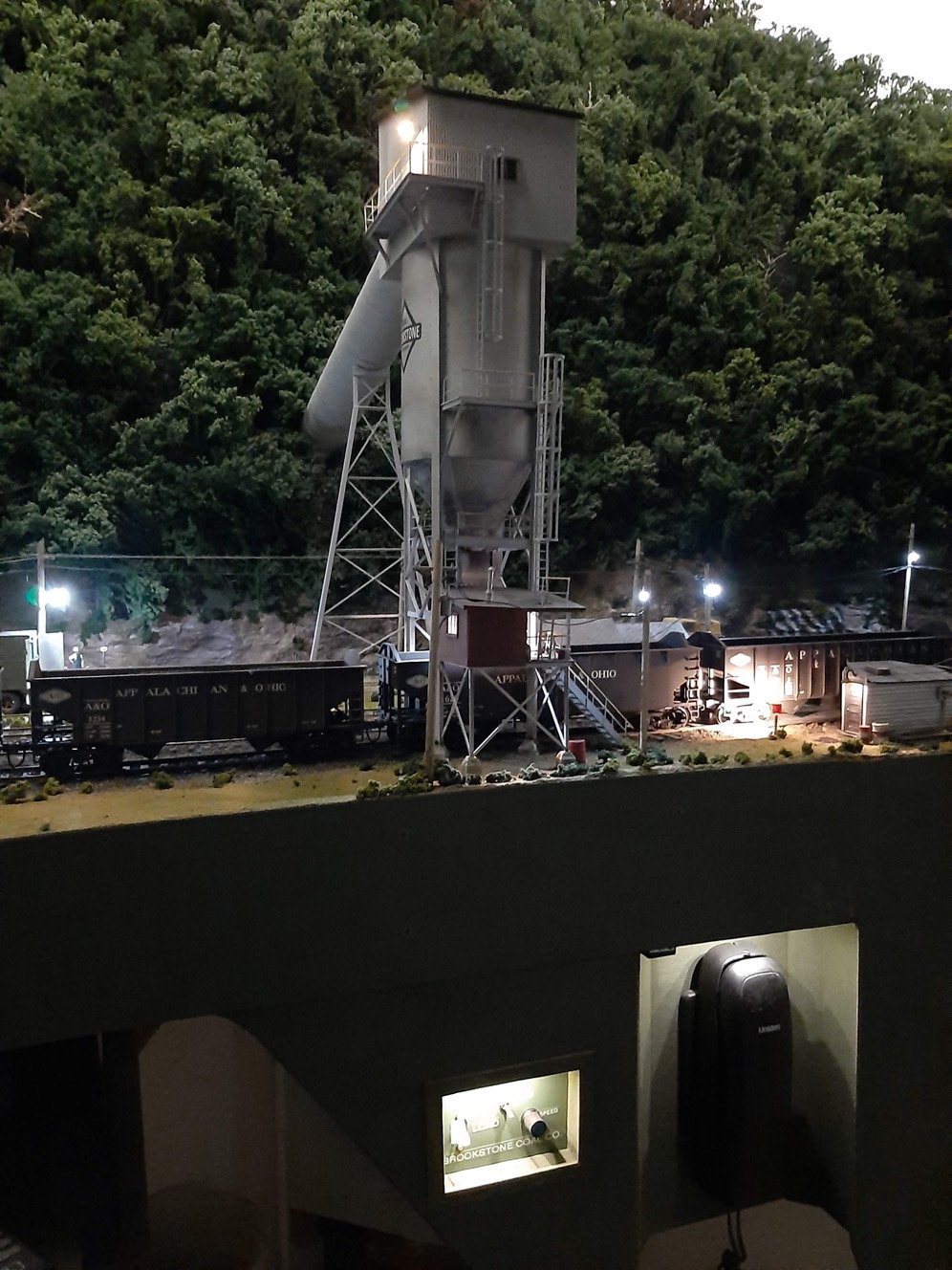
